Robotics and Automation for Water Exploration and Leak Prevention
Water is one of the essential substances that endeavors for people to investigate and explore are never sufficient. About 71% of the earth is covered by water, mostly in seas and oceans. Observation of marine life and exploration of unknown environments with minimal disturbance can help us better understand the habitat we are living in. Moreover, we, humans, even can’t live without clean water. Thus, improving the working condition and health of the water supply pipe system is the underlying task humans have to face. One problem is in open water, while the other is in a confined pipe space. But these two researches are quite relevant inherently and they both outline our contributions in soft materials, embedded instrumentation, control theory, and design methodologies.
A. Robotic technologies for smart pipes, in-pipe inspection and repairs
A.1 Specific Application
The world has a major issue with the basis of life, water. By 2025, the United Nations predicts that nearly two billion people will be living in countries or regions with absolute water scarcity. Furthermore, there are added stresses. They include (i) effects of climate change, (ii) rising demand for water by many communities,(iii) water pipe leakage, (iv) inefficient water management, and (v) inefficient water utilization. Around the world, about 25-30% of fresh and clean water is leaked into the ground annually during distribution. In developing countries, water loss rates can be more than 40%. In addition, results of such water leaks can result in property damage, caving of streets and foundations, and water contamination. Inefficiency of water management amplifies losses through pipe leakages. Thus, reducing the non-revenue water to an acceptable level is crucial. Different sectors rely on water and are significantly affected by these issues. They include energy utility, agriculture, commercial, manufacturing industries in addition to residential. Such pipe leakage problems happen also in the gas distribution industry. For example, the state of Massachusetts in the US, loses more than 18% of the distributed natural gas due to the 3000 leaks that take place every year. Therefore, reliable and effective technologies must be developed and deployed to ensure the sustainability of water supply.
A.2 Innovative, outstanding and essential
Our efforts have focused on the development of advanced robotic technologies for pipes, pipe inspection and repairs. Our approach targets two objectives: (i) development of smart pipes and (ii) in-pipe robots. Smart pipes are pipes that are instrumented, equipped with computing and communication capabilities. They gather and transmit information that includes continuous health monitoring and pipe integrity, product flow inside the pipe, the exact location of needed inspection, maintenance or repair, etc. Innovative multi-layer sensors with finely tuned material properties within each layer are developed to increase the signal-to-noise ratio. A novel energy harvester adopting magnetohydrodynamics (MHD) is developed to power low-power sensor nodes. In-pipe robots, on the other hand, are specialized robots designed to maneuver inside a pipe and conduct various tasks. This is different from diagnosing or repairing water distribution pipes from outside of the pipe. State-of-the-art rehabilitation techniques require the use of heavy machinery and human labor. Such practices are time-consuming, expensive, and inefficient, requiring service interruption. Several advantages are thus inherent to in-pipe robots. For example, the internal surface of pipes is generally more ‘informative’ than the external surface. Corrosion, the number one reason for pipe outbreaks, takes place more frequently inside the pipes than outside. Detecting or analyzing the by-product of pipe corrosion, such as tubercles, with an in-pipe robot, can lead to more certain indicators of a pipe defect, even before the defect actually takes place. We successfully developed both passive and active robots for diversified tasks in the pipe. The active robots we designed to feature outperforming maneuverability, which is superior within the confined pipe space.
A.3 Specific application: describe its tangible results and reasons for its significance
A series of in-pipe robotic solutions were developed. The development of such specialized robots and their associated technologies started in 2008. These include an in-pipe locomotion robot, an in-pipe inspection robot, an in-pipe rehabilitation robot, an in-pipe energy harvester, on-board pipe inspection sensors, underground communication networks, and underground path planning schemes of robot swarms. The inspection robot, rehabilitation robot, and energy harvester are three outstanding examples that present tangible advancements in our research. In brief, our customized pipe-profile sensor and off-line localization algorithms, the inspection robot portrays the in-pipe profile accurately as it moves along the pipe, including both pipe obstructions and the presence of leaks. Operators can then decide if a pipe segment requires an imminent repair or if the condition falls under operating standards. With this predictive capability, the water department is able to perform pipe rehabilitation before damage takes place, preventing major expenses, service disruptions and, and more importantly, ensuring the safety and health of citizens. Upon successful identification of(potential) pipe-related hazards, the next step is to rehabilitate the defect area. Consumer health and safety are of prime importance.
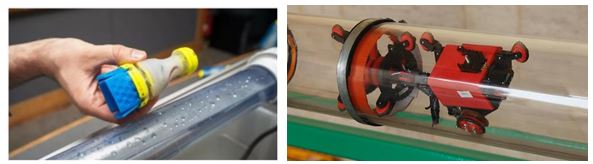
For example, here is an in-pipe robot that rehabilitates the pipe, contains the contamination while maintaining water service. Maintaining water service and water quality is desirable by customers and water departments. Manual pipe rehabilitation is also an abundant source for pipeline contamination, with corrosion in particular. The MRL rehabilitation robot aims at ameliorating pollution generated from the rehabilitation operation. It features a specialized robot configuration and a soft end effector to contain as much operational waste as possible. The advantage is obvious. By accessing the defect location from the inside, operators no longer have to conduct excessive digging and interrupt service. In addition, rehabilitation operations are far more efficient. In the case of traditional rehabilitation, the entire pipe section has to be replaced, even when the defect area is small. Alternatively, the in-pipe rehabilitation robot can localize the operation in this minimal area. Furthermore, robotic rehabilitation avoids the necessity to open-cut the pipe segment. This provides remarkable potentials that rehabilitation could be done even without shutting down the water distribution service.
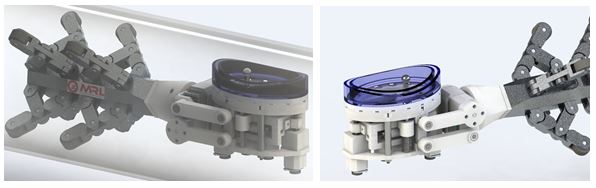
Designing and instrumenting auxiliary devices for in-pipe operation is a critical step towards the entire in-pipe industry. One outstanding example is our in-pipe energy harvester. We developed magnetohydrodynamics (MHD)based energy harvesters for low-power instrumentation. This innovative solution uses the water flow in the pipe to generate electrical power. Unlike traditional energy harvesters utilizing principles of electromagnetics, piezoelectricity, and solar energy conversion, the MHD energy harvester features a dramatic increase in robustness. This is essential in this application because of the ultra-long lifetime requirement of the pipe system. After careful analysis and design, our prototype MHD energy harvester demonstrates the potential to meet the power requirements of a sensor node with microcontrollers, sensors, communication, and data storage. This development provides a new perspective on energy harvesting and great confidence in self-contained instrumentation in the next generation of smart pipes.
Some other featured works are also noteworthy as important parts for the whole system to work. Sensing the robots location via GPS or remote sensors requires greater power and relies on certain ground properties. Thus we set out to localize the robot using only the onboard sensors which are an IMU, gyro, and the leak sensors. Through pipe joint measurement and the extended Kalman filter simulations show the tracking error is about 0.5% of the total distance of the robotic inspection. To better differentiate leaks from pipe joints and obstacles, sensors were arranged in a particular way to decouple the four deformation modes of the material: uniaxial tension, bending, compressive pressure, and torsion.
A.4 Playing an important role in human life
These developments have an important role in human life. Around 700 million people are suffering from water scarcity. The problem affects 43 counties from every continent on the earth. However, water scarcity is getting worse and worse. By 2025, absolute water scarcity will happen in the counties and regions where 1.8 billion people will be living. Two third of the global population will need to face stressed water conditions. And this ratio will increase to half by 2030. Even in regions with sufficient water supply, water quality is still a big concern. WHO reported that more than 3.4 million people are killed by water-related diseases around the world, making it the leading cause of disease and death. The smart pipes and in-pipe robots developed by us can effectively ameliorate the problem by monitoring and repairing the leak to make the utmost of the limited clean water supply, and monitoring water contamination in multiple forms to increase the water quality and control disease spread. Even in countries with sufficient and hygienic water supply, our research can further improve the efficiency of water utilization, boosting the development of industrial production and improvement of human life by lowering the cost of water supply.
B. Marine Robotics
B.1 Specific Application: Monitoring and predicting ocean health and marine life is crucial to the health of our planet. Conserving and renewing marine life to ensure a healthier planet.
As the saying goes Ocean health is our health. Covering more than 70% of the surface of our planet, oceans are the goldmines of natural resources. As technology advances, so does our step towards deep water. Underwater operations, such as oil well exploration, oil-spill monitoring, tactical reconnaissance involve strategic competitions between governments. With hydrologic monitoring of the ocean, such as the salinity, water temperature and dissolved oxygen, scientists are able to make predictions of the future states of various species. On the other hand, keeping track of the biological information of aqua-lives is also an accurate probe for scientists to observe the health of the ocean, or even, the health of our planet. [Ocean health to our health]
Even more resourceful and inspirational than the ocean is natural habitats in the ocean. For example, blue-fin tuna can reach a speed of ~74km/h, an extremely high speed even compared to modern ships that are proposed by steam or nuclear engines. The stamina of Atlantic salmon allows them to travel more than 10,000km before coming back home. How the naturally-evolved aqua-lives achieve such impressive engineering performances are of significant research value. To study the natural state of aqua-lives and protect our precious ocean, we, as observers, have to blend into the background. Looking and swimming like a fish is our solution.
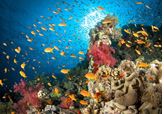
B.2 Innovative, outstanding and essential
Our work focused on the development of biomimetic robots for monitoring ocean health and marine life in their natural state. The MRL is the first to apply and formalize the basic principles of the underactuated soft body approach to fish-like robots. The approach relies on two principles: using soft bodies instead of traditional stiff mechanisms, and allowing passive mechanism dynamics to achieve target motions. With analytical modeling of desired swimming motion and combining it with the viscoelastic dynamics of the soft body in fluid, we can optimize the geometrical and material properties, such as the modulus of soft material and viscosity distribution of the fish body, and prescribe the actuation distribution, including actuator number, locations, magnitude, and frequency. Our design methodology is universal. We successfully applied the design to carangiform and thunniform-like bodies and later transferred to much more complex body forms such as batoid-like robots, like stingrays, and salamander bodies. Our robot takes full advantage of soft materials and swimming posture of fish, allowing us to significantly reduce the mechanical complexity of the robot while generating a more natural motion than previously proposed robots. Our research work also pioneered in characterization of and fabrication with soft materials like silicone rubber.
B.3 Specific application
A diversity of robotic fish were developed and field-tested. With our universal design methodology described above, we were able to propose and implement soft robotic fish of various body shapes. In one of our research articles, we detailed the development of a carangiform fish. Despite the kinematic and dynamic equations, we also set up a constrained optimization problem, such as minimizing the number of actuators, actuation amplitude or energy consumption. The finalized design is in a form of servo-actuated rigid plate, embodied in a viscoelastic body. To handle the fabrication of this unique design, we invented a sequential molding practice. The prototyped soft robotic fish was experimented in a laboratory environment. Our data acquisition system tracks the trajectories of multiple points on the robot’s body, collects the thrust, velocity, and visualizes the vortex flow at the vicinity of the fish. Additionally, we generalize the work to fish with even more complex geometries. One of our famous works is the stingray prototype. We conducted a field test with the stingray robot in Singapore.
B.4 Playing an important role in human life
These developments have an important role in human life. Our development in bio-inspired soft robotic fish plays an important role in human life. Scientists and engineers can now study and observe marine lives more intimately and quietly than ever before. Potentially, with our naturally-motioned robots, we will be able to manipulate the behavior of marine lives, or even perform in a leadership role. Such applications include steering fish away from environmental disaster, or balancing regional populations of various species. From an engineering point of view, the underactuated natural and its related control, fabrication, and mechanical design are inspirational to related researches. The efficient propulsion methodology of fish and unique usage of soft material are also heuristics to other marine robot locomotions or under-water vehicle designs. It motivated one of the MRL in-pipe locomotion robots in a later study.
C. Influence of the work:
C.1 important scientific contributions and advancement of knowledge
Our work has resulted in important scientific contributions. As a result, in the journey of this project till now, we have published 50 papers and disclosed 18 patents. The papers and patents range from sensor design and analysis, robot design, localization, communication, network management, and system integration. We also composed one book comprehensively covering not only the locomotion, actuation, design, soft material, and control, but also robotic fish collaboration and robot fish in animal behavioral studies. All these publications contribute cutting edge knowledge to academia and industry and provide priceless experience for enthusiasts working on soft materials, robotics, mechatronics, fluid-structure-interaction, and artificial intelligence. Dr. You Wu, the main developer of the leak detection soft robot, is honored with the following awards:
- 1) 2017 MIT Water Innovation Prize, this a startup competition focused on water innovation that awards up to $30K in innovation grants annually to student-led teams.
- 2) 2017 Infy maker Award by Infosys Foundation, Infy Maker Awards is a competition hosted by Infosys Foundation USA.
- Environmental Media Association, 2018, The Environmental Media Association (EMA) is dedicated to the mission of promoting environmental progress and bring the planet’s most pressing issues to the forefront.
- 3) Future Innovator Award, 2018 James Dyson Award, and many others.
- 4) Forbes 30 Under 30, one of four MIT students in 2018 to receive this title even before his graduation.
In addition to the awards, our in-pipe leak detection robots were featured on the Business Insider, Quartz, the MIT News for twice, and several other reputational press in the US. Our marine robot is reported by the discovery channel, CNN, and MIT news.
Our research has advanced the frontiers of knowledge. Besides the key technologies we developed during the journey, we proposed several methodologies for sensors, soft material modelings, design, robotics, and several other fields. With these methodologies and experience, we promote our research faster and faster. For example, in the development of the marine robot, we identified and summarized a five-step design methodology for soft robotic fish. And in most of our researches, we combine theoretical analysis, modeling, numerical simulation, fast prototyping, and testing.
C.2 Our work had a great impact
After successful development in the lab phase, we gradually ramped up our field test, industrial collaboration, and commercialization to pursue a greater impact. We first collaborated with Singapore on the robot fish. Later, we collaborated with Saudi Arabia to perform the test of our leak detection soft robot in a well-established above-ground pipe system. The results are promising that even premature leaks with a small flow volume can be distinguished and trigger the alarm. After that, we were invited by the water authorities of Cambridge, Virginia, Brazil, and the UK to perform field tests in real pipe systems that supply water to households. The results are satisfying. Several leaks were detected successfully, and the water authorities avoided the huge economic loss and potential service interruption. With these field tests, the adaptability of the robot to various working conditions, pipe materials, pipe sizes, and flow volumes is demonstrated. With the experience of the successful field tests, a startup called watchtower is launched by Dr. You Wu, who graduated from MRL.
When working on the problem, we bear in mind that generality is also a top priority besides efficacy. Most principles we investigate and dive into are generic. Thus the technologies and breakthrough we contributed can also be applied to some other industries with similar problems. For example, Massachusetts in the US loses about $100M per year due to the natural gas leak. The petrochemical companies, which rely heavily on pipe systems to deliver the material and products, also encounter the similar problems of a pipe leak, pipe burst, and pipe corrosion. The leak detection sensors sense the pressure gradient around the leaks, which is a common phenomenon for fluid with high pressure inside an enclosed space. The seal and machinery cleaning mechanisms are also generic for hard surfaces. Thus adopting these technologies in other industries is a pushover. The generic solutions to our research make our innovation much more impactful.
2019
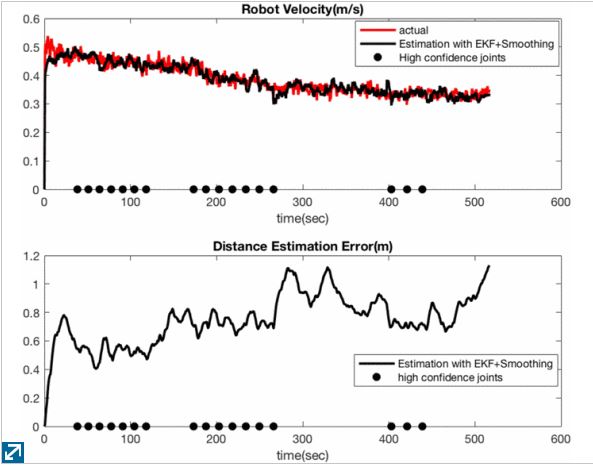
You Wu; Elizabeth Mittmann; Crystal Winston; Kamal Youcef-Toumi
A Practical Minimalism Approach to In-pipe Robot Localization Proceedings Article
In: 2019 American Control Conference (ACC), pp. 3180-3187, IEEE IEEE, 2019, ISBN: 978-1-5386-7926-5.
@inproceedings{MRL_WDP_Pipe_Robot_Localization,
title = {A Practical Minimalism Approach to In-pipe Robot Localization},
author = {You Wu and Elizabeth Mittmann and Crystal Winston and Kamal Youcef-Toumi},
url = {https://ieeexplore.ieee.org/document/8814648},
doi = {10.23919/ACC.2019.8814648},
isbn = {978-1-5386-7926-5},
year = {2019},
date = {2019-08-19},
booktitle = {2019 American Control Conference (ACC)},
pages = {3180-3187},
publisher = {IEEE},
organization = {IEEE},
abstract = {Water pipe leakage is a common and significant problem around the world. In recent years, an increasing amount of effort has been put into developing effective leak detection solutions for water pipes. Among them, the pressure gradient based method developed at the Massachusetts Institute of Technology excels for its sensitivity in low pressure, small diameter pipes. It can also work in both plastic and metallic pipes. However, in order for leaks detected to be fixed, one must also know the locations of the leaks. In addition, sensing the robot's location via GPS or remote sensors requires greater power and relies on certain ground properties. Thus this paper sets out to localize the robot using only the on board sensors which are an IMU, gyro, and the leak sensors. Through pipe joint measurement and the extended Kalman filter simulations show the tracking error is about 0.5% of the total distance of the robotic inspection. With a minimal number of additional leak sensors added, a complementary method was developed to function in more heavily tuberculated pipes.},
keywords = {},
pubstate = {published},
tppubtype = {inproceedings}
}
2017
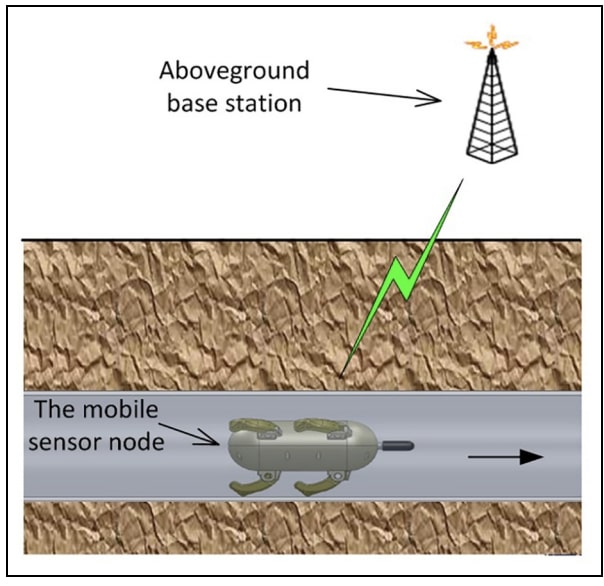
S Mekid; D Wu; R Hussain; K Youcef-Toumi
Channel modeling and testing of wireless transmission for underground in-pipe leak and material loss detection Journal Article
In: International Journal of Distributed Sensor Networks, vol. 13, no. 11, pp. 1550147717744715, 2017, ISSN: 1550147717744715.
@article{MRL_AFM_Channel_Modeling,
title = {Channel modeling and testing of wireless transmission for underground in-pipe leak and material loss detection},
author = {S Mekid and D Wu and R Hussain and K Youcef-Toumi},
url = {https://doi.org/10.1177/1550147717744715},
doi = {10.1177/1550147717744715},
issn = {1550147717744715},
year = {2017},
date = {2017-01-01},
journal = {International Journal of Distributed Sensor Networks},
volume = {13},
number = {11},
pages = {1550147717744715},
publisher = {Sage},
abstract = {A systematic real-time methodology is adopted for leak detection in underground buried pipes. The wireless communication system is used to analyze the system performance based on the received power by monopole antenna deployed at the receiving side. Instrumentation designed for underground measurement and control such as leak and materials loss detection needs wireless communications to aboveground in both ways and in real-time mode. This constitutes one of the timely and challenging issues of battery-operated systems. The purpose of this work is to characterize the radio transmission between underground buried pipes and base station using multi-layer media including both theoretical and experimental approaches by utilizing various modulation schemes. The objective is to identify the range of operating communication frequencies having lower energy loss, lower resulting bit error rate, and the power needed to transfer packets designed to carry data through the media. This will support the on-device power management to secure large autonomy operations. Experimental tests have shown that the overall received energy was mixed with ambient energy if the latter is sent at the same frequency and that the optimum frequency range used to transmit energy was rather at low frequency range of 100–200 MHz.},
keywords = {},
pubstate = {published},
tppubtype = {article}
}
2015
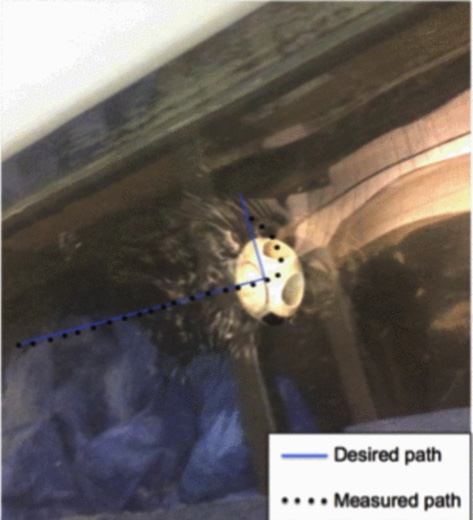
You Wu; Antoine Noel; David Donghyun Kim; Kamal Youcef-Toumi; Rached Ben-Mansour
Design of a maneuverable swimming robot for in-pipe missions Proceedings Article
In: 2015 IEEE/RSJ International Conference on Intelligent Robots and Systems (IROS), pp. 4864-4871, IEEE IEEE, 2015, ISBN: 978-1-4799-9994-1.
@inproceedings{MRL_WDP_In_Pipe_Missions,
title = {Design of a maneuverable swimming robot for in-pipe missions},
author = {You Wu and Antoine Noel and David Donghyun Kim and Kamal Youcef-Toumi and Rached Ben-Mansour},
url = {https://ieeexplore.ieee.org/document/7354061},
doi = {10.1109/IROS.2015.7354061},
isbn = {978-1-4799-9994-1},
year = {2015},
date = {2015-12-17},
booktitle = {2015 IEEE/RSJ International Conference on Intelligent Robots and Systems (IROS)},
pages = {4864-4871},
publisher = {IEEE},
organization = {IEEE},
abstract = {Autonomous underwater robots provide opportunities to perform missions in confined environments such as water pipe networks. They can carry sensors in these pipes and perform tasks such as mapping and inspection. Those robots must have a high level of maneuverability in order to navigate through complex networks of pipes with irregularities due to rust and calcite deposition. We propose a fully integrated, untethered robot capable of carrying sensors and maneuver into water pipe networks. The objective of this paper is to present (i) the optimal shape design and (ii) a propulsion system selection and sizing procedure for such robots. A prototype is built to demonstrate the basic elements of maneuverability, including following straight lines and making sharp turns.},
keywords = {},
pubstate = {published},
tppubtype = {inproceedings}
}
2014
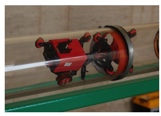
Dimitris Chatzigeorgiou; You Wu; Kamal Youcef-Toumi; Rached Ben-Mansour
MIT Leak Detector: An in-pipe leak detection robot Proceedings Article
In: 2014 IEEE International Conference on Robotics and Automation (ICRA), pp. 2091-2091, IEEE IEEE, 2014, ISBN: 978-1-4799-3685-4.
@inproceedings{MRL_WDP_Leak_Detecting_Robot,
title = {MIT Leak Detector: An in-pipe leak detection robot},
author = {Dimitris Chatzigeorgiou and You Wu and Kamal Youcef-Toumi and Rached Ben-Mansour},
url = {https://ieeexplore.ieee.org/document/6907144},
doi = {10.1109/ICRA.2014.6907144},
isbn = {978-1-4799-3685-4},
year = {2014},
date = {2014-09-24},
booktitle = {2014 IEEE International Conference on Robotics and Automation (ICRA)},
pages = {2091-2091},
publisher = {IEEE},
organization = {IEEE},
abstract = {In this work we present a new in-pipe leak detection robot, the MIT Leak Detector. The system performs autonomous leak detection in gas pipes in a reliable and robust fashion. Detection in based on the presence of a pressure gradient in the neighborhood of the leak. As the MIT Leak Detector travels through pipes, it picks up the pressure gradient in case of leaks via a carefully designed detector. In this work we demonstrate the performance of the system in a lab setup, which consists of 100mm ID pipes containing pressurized air.},
keywords = {},
pubstate = {published},
tppubtype = {inproceedings}
}
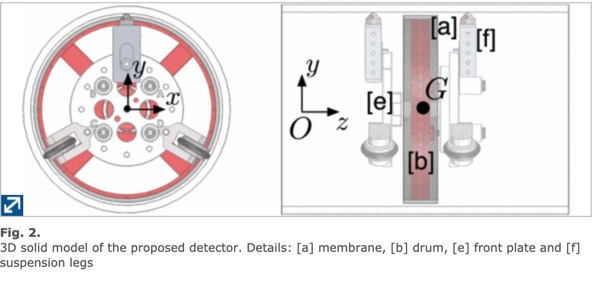
Dimitris Chatzigeorgiou; Kamal Youcef-Toumi; Rached Ben-Mansour
Modeling and analysis of an in-pipe robotic leak detector Proceedings Article
In: 2014 IEEE International Conference on Robotics and Automation (ICRA), pp. 3351-3357, IEEE, 2014, ISBN: 978-1-4799-3685-4.
@inproceedings{MRL_WDP_Analysis_Leak_Detection,
title = {Modeling and analysis of an in-pipe robotic leak detector},
author = {Dimitris Chatzigeorgiou and Kamal Youcef-Toumi and Rached Ben-Mansour},
url = {https://ieeexplore.ieee.org/abstract/document/6907341},
doi = {10.1109/ICRA.2014.6907341},
isbn = {978-1-4799-3685-4},
year = {2014},
date = {2014-09-24},
booktitle = {2014 IEEE International Conference on Robotics and Automation (ICRA)},
pages = {3351-3357},
publisher = {IEEE},
abstract = {Leakage is the most important factor for unaccounted losses in any pipe network around the world. Most state of the art leak detection systems have limited applicability, lack in reliability and depend on user experience for data extraction. This paper is about a novel system for robotic pipe integrity inspection. Unlike existing systems, detection in based on the presence of a pressure gradient in the neighborhood of a leak. This phenomenon is translated into force measurements via a specially designed and instrumented mechanical embodiment (detector). In this paper an analytic dynamic model of the robotic detector is derived and studied. A prototype is built and the main concepts are validated via experiments.},
keywords = {},
pubstate = {published},
tppubtype = {inproceedings}
}
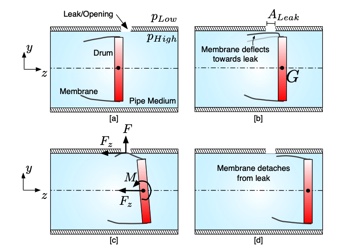
Dimitris Chatzigeorgiou; Kamal Youcef-Toumi; Rached Ben-Mansour
Detection estimation algorithms for in-pipe leak detection Proceedings Article
In: 2014 American Control Conference, pp. 5508-5514, 2014, ISBN: 978-1-4799-3274-0.
@inproceedings{MRL_WDP_Estimation_Algorithms,
title = {Detection estimation algorithms for in-pipe leak detection},
author = {Dimitris Chatzigeorgiou and Kamal Youcef-Toumi and Rached Ben-Mansour},
url = {https://ieeexplore.ieee.org/document/6859203},
doi = {10.1109/ACC.2014.6859203},
isbn = {978-1-4799-3274-0},
year = {2014},
date = {2014-07-21},
booktitle = {2014 American Control Conference},
pages = {5508-5514},
abstract = {Leakage is the most important factor for unaccounted losses in any pipe network around the world. However, most state of the art leak detection systems have limited applicability, lack in reliability and/or depend on user experience for data interpretation. In this paper we present a new, autonomous, in-pipe, leak detection system. The detection principle is based on the presence of a pressure gradient in the neighborhood of a leak in a pressurized pipe. This phenomenon is translated into force measurements via a carefully designed and instrumented mechanical embodiment (MIT Leak Detector). We then introduce a detection and estimation scheme. The latter one allows not only for the reliable detection, but also for the estimation of the incidence angle and the magnitude of the forces that are associated with the leak. Finally, a prototype is built and experiments in pipes are conducted to demonstrate the efficacy of the proposed methodology.},
keywords = {},
pubstate = {published},
tppubtype = {inproceedings}
}
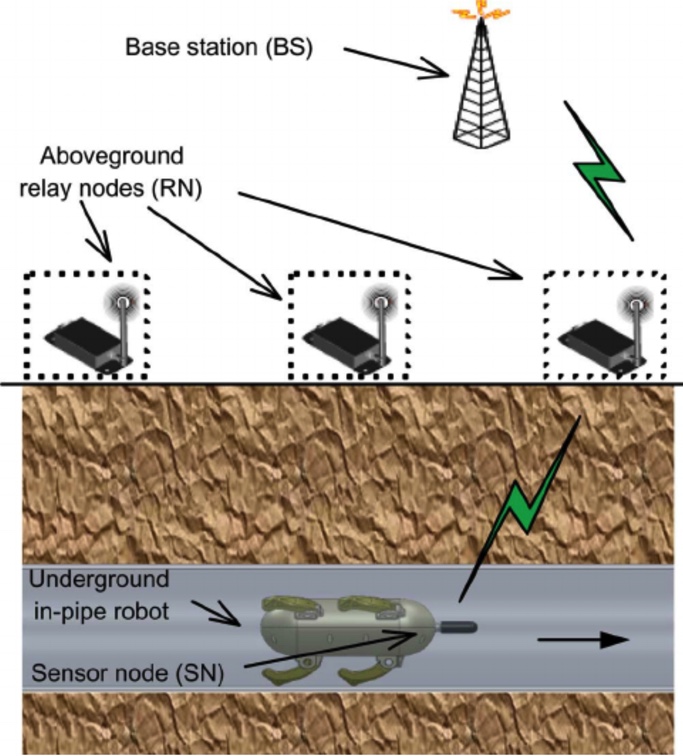
Dalei Wu; Dimitris Chatzigeorgiou; Kamal Youcef-Toumi; Samir Mekid; Rached Ben-Mansour
Channel-Aware Relay Node Placement in Wireless Sensor Networks for Pipeline Inspection Proceedings Article
In: Proceedings of the American Control Conference (2013), ACC ACC, 2014, ISSN: 1536-1276.
@inproceedings{MRL_WDP_Node_Pipeline_Inspection,
title = {Channel-Aware Relay Node Placement in Wireless Sensor Networks for Pipeline Inspection},
author = {Dalei Wu and Dimitris Chatzigeorgiou and Kamal Youcef-Toumi and Samir Mekid and Rached Ben-Mansour},
url = {https://www.researchgate.net/publication/261282962_Channel-Aware_Relay_Node_Placement_in_Wireless_Sensor_Networks_for_Pipeline_Inspection},
doi = {10.1109/TWC.2014.2314120},
issn = {1536-1276},
year = {2014},
date = {2014-03-24},
booktitle = {Proceedings of the American Control Conference (2013)},
publisher = {ACC},
organization = {ACC},
abstract = {Wireless sensor networks (WSNs) provide an effective approach for underground pipeline inspection. Such WSNs comprise of sensor nodes (SNs) and relay nodes (RNs) for information sensing and communication. WSNs can perform accurate and realtime inspection, especially in adverse environments. However, transmitting information between underground and aboveground nodes is very challenging due to the mobility and limited energy supply of the SNs as well as complex radio propagation environment. Therefore, proper deployment of a WSN is critical to provide reliable communications and efficient inspection. This paper presents a methodology for deploying aboveground RNs in WSNs. Specifically, it provides an optimum placement of RNs along with energy use so as to allow reliable communications. This method takes into account characteristics of the wireless channels, energy consumption, pipeline coverage requirements, and SN's transmission power levels. The paper provides a path loss model for radio propagation over multiple transmission media and an algorithm for optimization of RN placement and SN's transmission power. Simulation results show the efficacy of the proposed framework.},
keywords = {},
pubstate = {published},
tppubtype = {inproceedings}
}
2013
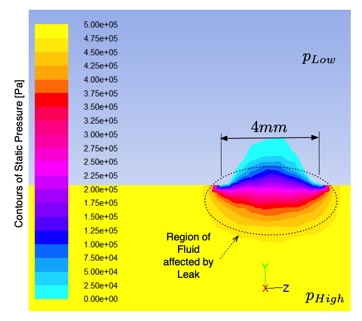
Apoorva Santhosh; Amro M Farid; Kamal Youcef-Toumi
Design and Evaluation of an In-Pipe Leak Detection Sensing Technique Based on Force Transduction Proceedings Article
In: ASME 2012 International Mechanical Engineering Congress and Exposition, IEEE IEEE, 2013, ISBN: 978-0-7918-4520-2.
@inproceedings{MRL_WDP_Force_Transduction_Leaking,
title = {Design and Evaluation of an In-Pipe Leak Detection Sensing Technique Based on Force Transduction},
author = {Apoorva Santhosh and Amro M Farid and Kamal Youcef-Toumi},
url = {https://asmedigitalcollection.asme.org/IMECE/proceedings/IMECE2012/45202/489/254570},
doi = {10.1115/IMECE2012-87493},
isbn = {978-0-7918-4520-2},
year = {2013},
date = {2013-10-08},
booktitle = {ASME 2012 International Mechanical Engineering Congress and Exposition},
publisher = {IEEE},
organization = {IEEE},
abstract = {Leakage is the major factor for unaccounted fluid losses in almost every pipe network. In most cases the deleterious effects associated with the occurrence of leaks may present serious economical and health problems and therefore, leaks must be quickly detected, located and repaired. The problem of leakage becomes even more serious when it is concerned with the vital supply of fresh water to the community. Leaking water pipelines can develop large health threats to people mostly because of the infiltration of contaminants into the water network. Such possibilities of environmental health disasters have spurred research into the development of methods for pipeline leakage detection. Most state of the art leak detection techniques have limited applicability, while some of them are not reliable enough and sometimes depend on user experience. Our goal in this work is to design and develop a reliable leak detection sensing system. The proposed technology utilizes the highly localized pressure gradient in the vicinity of a small opening due to leakage in a pressurized pipeline. In this paper we study this local phenomenon in detail and try to understand it with the help of numerical simulations in leaking pipelines (CFD studies). Finally a new system for leak detection is presented. The proposed system is designed in order to reduce the number of sensing elements required for detection. The main concept and detailed design are laid out. A prototype is fabricated and presented as a proof of concept. The prototype is tested in a simple experimental setup with artificial leakages for experimental evaluation. The sensing technique discussed in this work can be deployed in water, oil and gas pipelines without significant changes in the design, since the concepts remain the same in all cases.},
keywords = {},
pubstate = {published},
tppubtype = {inproceedings}
}
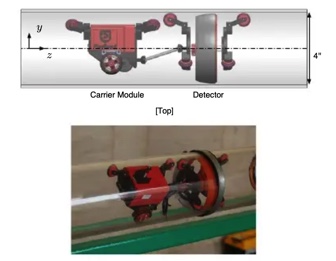
Dimitris Chatzigeorgiou; You Wu; Kamal Youcef-Toumi; Rached Ben-Mansour
Reliable Sensing of Leaks in Pipelines Proceedings Article
In: AWWA Annual Conference and Exposition, 2014, ASME ASME, 2013, ISBN: 978-0-7918-5613-0.
@inproceedings{MRL_WDP_Reliable_Leak_Sensing,
title = {Reliable Sensing of Leaks in Pipelines},
author = {Dimitris Chatzigeorgiou and You Wu and Kamal Youcef-Toumi and Rached Ben-Mansour},
url = {https://www.academia.edu/8791279/Chatzigeorgiou_D._Wu_Y._Youcef-Toumi_K._and_Ben-Mansour_R._Reliable_Sensing_of_Leaks_in_Pipelines_ASME_Dynamic_Systems_and_Control_Conference_2013},
isbn = {978-0-7918-5613-0},
year = {2013},
date = {2013-01-01},
booktitle = {AWWA Annual Conference and Exposition, 2014},
publisher = {ASME},
organization = {ASME},
abstract = {Leakage is the major factor for unaccounted losses in every pipe network around the world (oil, gas or water). In most cases the deleterious effects associated with the occurrence of leaks may present serious economical and health problems. Therefore, leaks must be quickly detected, located and repaired. Unfortunately, most state of the art leak detection systems have limited applicability, are neither reliable nor robust, while others depend on user experience. In this work we present a new in-pipe leak detection system, PipeGuard. PipeGuard performs autonomous leak detection in pipes and, thus, eliminates the need for user experience. This paper focuses on the detection module and its main characteristics. Detection in based on the presence of a pressure gradient in the neighborhood of the leak. Moreover, the proposed detector can sense leaks at any angle around the circumference of the pipe with only two sensors. We have validated the concepts by building a prototype and evaluated its performance under real conditions in an experimental laboratory setup.},
keywords = {},
pubstate = {published},
tppubtype = {inproceedings}
}
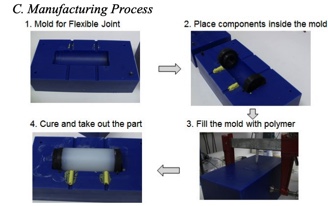
Changrak Choi; Kamal Youcef-Toumi
Robot design for high flow liquid pipe networks Proceedings Article
In: 2013 IEEE/RSJ International Conference onIntelligent Robots and Systems (IROS), pp. 246-251, IEEE IEEE, 2013.
@inproceedings{MRL_WDP_High_Flow_Pipe_Robot,
title = {Robot design for high flow liquid pipe networks},
author = {Changrak Choi and Kamal Youcef-Toumi},
url = {https://ieeexplore.ieee.org/stamp/stamp.jsp?tp=&arnumber=6696360&isnumber=6696319},
doi = {10.1109/IROS.2013.6696360},
year = {2013},
date = {2013-01-01},
booktitle = {2013 IEEE/RSJ International Conference onIntelligent Robots and Systems (IROS)},
pages = {246-251},
publisher = {IEEE},
organization = {IEEE},
abstract = {In-pipe robots are important for inspection of pipe network that form vital infrastructure of modern society. Nevertheless, most in-pipe robots developed so far are targeted at working inside gas pipes and not suitable for liquid pipes. This paper presents a new approach for designing in-pipe robot to work inside a liquid environment in the presence of high drag forces. Three major subsystems - propulsion, braking, and turning - are described in detail with new concepts and mechanisms that differ from conventional in-pipe robots. Prototypes of each subsystem are designed, built and tested for validation. Resulting is a robot design that navigates efficiently inside liquid pipe network and can be used for practical inspection purposes.},
keywords = {},
pubstate = {published},
tppubtype = {inproceedings}
}
2012
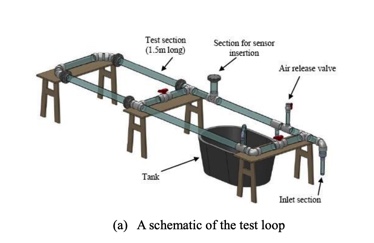
Atia E Khalifa; Rached Ben-Mansour; Kamal Youcef-Toumi; Changrak Choi
Characterization of In-Pipe Acoustic Wave for Water Leak Detection Proceedings Article
In: ASME 2011 International Mechanical Engineering Congress and Exposition, pp. 995-1000, ACC ACC, 2012, ISBN: 978-0-7918-5494-5.
@inproceedings{MRL_WDP_Acoustic_Wave_Pipe_Leakage,
title = {Characterization of In-Pipe Acoustic Wave for Water Leak Detection},
author = {Atia E Khalifa and Rached Ben-Mansour and Kamal Youcef-Toumi and Changrak Choi},
url = {https://asmedigitalcollection.asme.org/IMECE/proceedings/IMECE2011/54945/995/355499},
doi = {10.1115/IMECE2011-62333},
isbn = {978-0-7918-5494-5},
year = {2012},
date = {2012-08-01},
booktitle = {ASME 2011 International Mechanical Engineering Congress and Exposition},
pages = {995-1000},
publisher = {ACC},
organization = {ACC},
abstract = {This paper presents experimental observations on the characteristics of the acoustic signal propagation and attenuation inside water-filled pipes. An acoustic source (exciter) is mounted on the internal pipe wall, at a fixed location, and produces a tonal sound to simulate a leak noise with controlled frequency and amplitude, under different flow conditions. A hydrophone is aligned with the pipe centerline and can be re-positioned to capture the acoustic signal at different locations. Results showed that the wave attenuation depends on the source frequency and the line pressure. High frequency signals get attenuated more with increasing distance from the source. The optimum location to place the hydrophone for capturing the acoustic signal is not at the vicinity of source location. The optimum location also depends on the frequency and line pressure. It was also observed that the attenuation of the acoustic waves is higher in more flexible pipes like PVC ones.},
keywords = {},
pubstate = {published},
tppubtype = {inproceedings}
}
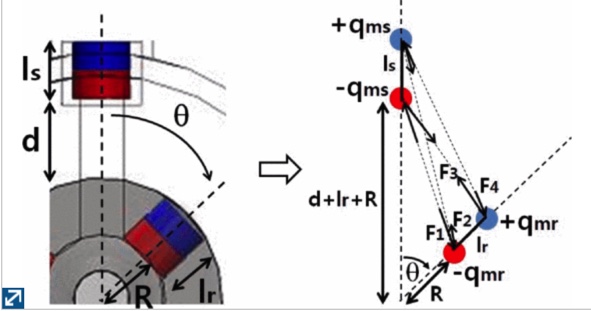
C Choi; D Chatzigeorgiou; R Ben-Mansour; K Youcef-Toumi
Design and analysis of novel friction controlling mechanism with minimal energy for in-pipe robot applications Proceedings Article
In: 2012 IEEE International Conference on Robotics and Automation, pp. 4118-4123, IEEE IEEE, 2012, ISBN: 978-1-4673-1405-3.
@inproceedings{MRL_WDP_Friction_Minimization,
title = {Design and analysis of novel friction controlling mechanism with minimal energy for in-pipe robot applications},
author = {C Choi and D Chatzigeorgiou and R Ben-Mansour and K Youcef-Toumi},
url = {https://ieeexplore.ieee.org/document/6225380},
doi = {10.1109/ICRA.2012.6225380},
isbn = {978-1-4673-1405-3},
year = {2012},
date = {2012-06-28},
booktitle = {2012 IEEE International Conference on Robotics and Automation},
pages = {4118-4123},
publisher = {IEEE},
organization = {IEEE},
abstract = {In-pipe wheeled robots require friction on the wheels to maintain traction. Ability to vary this friction is highly desirable but conventionally used linkage mechanism is not suitable for it. This paper presents a novel mechanism generating adjustable friction with minimal energy consumption for in-pipe robots. The mechanism uses permanent magnets to achieve the objective. An appropriate model for the system is also presented and discussed. The paper identifies the important design parameters, and more importantly establishes the relation between the design parameters and the system's performance. In addition, a prototype of the mechanism was designed, fabricated and tested for validation.},
keywords = {},
pubstate = {published},
tppubtype = {inproceedings}
}
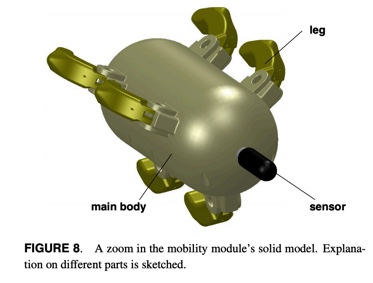
Dimitris M Chatzigeorgiou; Atia E Khalifa; Kamal Youcef-Toumi; Rached Ben-Mansour
An In-Pipe Leak Detection Sensor: Sensing Capabilities and Evaluation Proceedings Article
In: ASME 2011 International Design Engineering Technical Conferences and Computers and Information in Engineering Conference, pp. 481-489, ACC ACC, 2012, ISBN: 978-0-7918-5480-8.
@inproceedings{MRL_WDP_Leak_Capability_Sensor,
title = {An In-Pipe Leak Detection Sensor: Sensing Capabilities and Evaluation},
author = {Dimitris M Chatzigeorgiou and Atia E Khalifa and Kamal Youcef-Toumi and Rached Ben-Mansour},
url = {https://asmedigitalcollection.asme.org/IDETC-CIE/proceedings/IDETC-CIE2011/54808/481/351961},
doi = {10.1115/DETC2011-48411},
isbn = {978-0-7918-5480-8},
year = {2012},
date = {2012-06-12},
booktitle = {ASME 2011 International Design Engineering Technical Conferences and Computers and Information in Engineering Conference},
pages = {481-489},
publisher = {ACC},
organization = {ACC},
abstract = {In most cases the deleterious effects associated with the occurrence of leak may present serious problems and therefore leaks must be quickly detected, located and repaired. The problem of leakage becomes even more serious when it is concerned with the vital supply of fresh water to the community. In addition to waste of resources, contaminants may infiltrate into the water supply. The possibility of environmental health disasters due to delay in detection of water pipeline leaks has spurred research into the development of methods for pipeline leak and contamination detection. Leaks in water pipes create acoustic emissions, which can be sensed to identify and localize leaks. Leak noise correlators and listening devices have been reported in the literature as successful approaches to leak detection but they have practical limitations in terms of cost, sensitivity, reliability and scalability. To overcome those limitations the development of an in-pipe traveling leak detection system is proposed. The development of such a system requires a clear understanding of acoustic signals generated from leaks and the study of the variation of those signals with different pipe loading conditions, leak sizes and surrounding media. This paper discusses those signals and evaluates the merits of an in-pipe-floating sensor.},
keywords = {},
pubstate = {published},
tppubtype = {inproceedings}
}
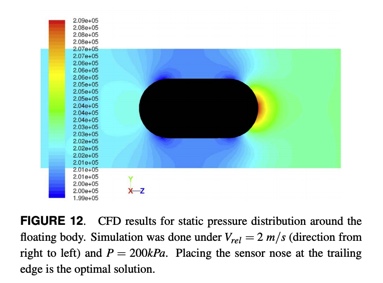
Dimitris M Chatzigeorgiou; Kamal Youcef-Toumi; Atia E Khalifa; Rached Ben-Mansour
Analysis and Design of an In-Pipe System for Water Leak Detection Proceedings Article
In: ASME 2011 International Design Engineering Technical Conferences and Computers and Information in Engineering Conference, pp. 1007-1016, ASME ASME, 2012, ISBN: 978-0-7918-5482-2.
@inproceedings{MRL_WDP_Design_Water_Leak_Detection,
title = {Analysis and Design of an In-Pipe System for Water Leak Detection},
author = {Dimitris M Chatzigeorgiou and Kamal Youcef-Toumi and Atia E Khalifa and Rached Ben-Mansour},
url = {https://asmedigitalcollection.asme.org/IDETC-CIE/proceedings/IDETC-CIE2011/54822/1007/353866},
doi = {10.1115/DETC2011-48395},
isbn = {978-0-7918-5482-2},
year = {2012},
date = {2012-06-12},
booktitle = {ASME 2011 International Design Engineering Technical Conferences and Computers and Information in Engineering Conference},
pages = {1007-1016},
publisher = {ASME},
organization = {ASME},
abstract = {In most cases the deleterious effects associated with the occurrence of leaks may present serious problems and therefore, leaks must be quickly detected, located and repaired. The problem of leakage becomes even more serious when it is concerned with the vital supply of fresh water to the community. In addition to waste of resources, contaminants may infiltrate into the water supply. The possibility of environmental health disasters due to delay in detection of water pipeline leaks has spurred research into the development of methods for pipeline leak and contamination detection. Leaking in water networks has been a very significant problem worldwide, especially in developing countries, where water is sparse. Many different techniques have been developed to detect leaks, either from the inside or from the outside of the pipe; each one of them with their advantages, complexities but also limitations. To overcome those limitations we focus our work on the development of an in-pipe-floating sensor. The present paper discusses the design considerations of a novel autonomous system for in-pipe water leak detection. The system is carefully designed to be minimally invasive to the flow within the pipe and thus not to affect the delicate leak signal. One of its characteristics is the controllable motion inside the pipe. The system is capable of pinpointing leaks in pipes while operating in real network conditions, i.e. pressurized pipes and high water flow rates, which are major challenges.},
keywords = {},
pubstate = {published},
tppubtype = {inproceedings}
}
2010
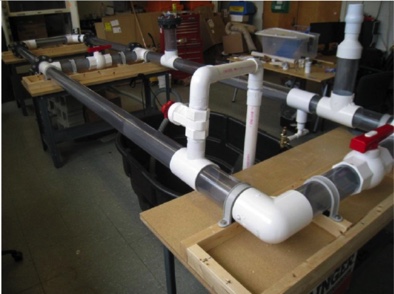
Dimitris M Chatzigeorgiou; Sumeet Kumar; Atia E Khalifa; Ajay Deshpande; Kamal Youcef-Toumi; Sanjay Sarma; Rached Ben-Mansour
In-pipe Acoustic Characterization of Leak Signals in Plastic Water-filled Pipes Proceedings Article
In: AWWA Annual Conference and Exposition (ACE) 2010, AWWA AWWA, 2010.
@inproceedings{MRL_WDP_Acoustic_Leak_Signals,
title = {In-pipe Acoustic Characterization of Leak Signals in Plastic Water-filled Pipes},
author = {Dimitris M Chatzigeorgiou and Sumeet Kumar and Atia E Khalifa and Ajay Deshpande and Kamal Youcef-Toumi and Sanjay Sarma and Rached Ben-Mansour},
url = {https://www.researchgate.net/publication/277303127_In-pipe_Acoustic_Characterization_of_Leak_Signals_in_Plastic_Water-filled_Pipes},
year = {2010},
date = {2010-01-01},
booktitle = {AWWA Annual Conference and Exposition (ACE) 2010},
publisher = {AWWA},
organization = {AWWA},
abstract = {Acoustic emissions can be sensed to identify and localize leaks in water pipes. Leak noise correlators and listening devices have been reported in literature as successful approaches to leak detection but they have practical limitations in terms of cost, sensitivity, reliability and scalability. A possible efficient solution is the development of an in-pipe traveling leak detection system. It has been reported that in-pipe sensing is more accurate and efficient since the sensing element can be very close to the sound source. Currently in-pipe approaches are limited to large leaks and larger diameter pipes. Development of such a system requires clear understanding of acoustic signals generated from leaks and their variation with different pipe loading conditions, leak sizes and surrounding media. This paper discusses the acoustic characterization of leak signals in controlled environments. A lab experimental setup was designed and built in which measurements were taken from inside 4 inch PVC water pipes using a hydrophone. Signals were collected for a wide range of conditions: different pressures and leak flow rates to better understand the leak signal signatures. Experiments were conducted with different pipe connecting elements like valves and junctions, and different external conditions such as pipes placed in water, air and soil. Signals were collected at various distances from the leak location (upstream and downstream) to understand the opportunities of spatial cross-correlation techniques in localizing leaks and the effect of sensor position on the signal. Characterizations of different datasets are presented in frequency domain. The implications of acoustic characterization on the design of algorithms for leak detection are discussed and a simple algorithm to decide whether or not a leak is present near the sensor location is proposed, based on signal power calculations. The characterization gives insights, which will pave ways for the development of smart, autonomous pipe-traversing systems capable of detecting and localizing leaks on a city level water distribution network.},
keywords = {},
pubstate = {published},
tppubtype = {inproceedings}
}