Mechatronics Research Lab Publications
List still being populated due to webpage maintenance
2017
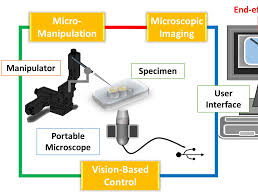
L Yang; I Paranawithana; K Youcef-Toumi; U Tan
Automatic Vision-Guided Micromanipulation for Versatile Deployment and Portable Setup Journal Article
In: IEEE Transactions on Automation Science and Engineering, vol. 15, no. 4, pp. 1609-1620, 2017, ISSN: 1558-3783.
Abstract | Links | BibTeX | Tags: Control Theory, Mechatronic Design, Physical System Modeling, Robot operated modular fixtures, Robotics & Automation
@article{MRL_AFM_Automatic_Micromanipulation,
title = {Automatic Vision-Guided Micromanipulation for Versatile Deployment and Portable Setup},
author = {L Yang and I Paranawithana and K Youcef-Toumi and U Tan},
doi = {10.1109/TASE.2017.2754517},
issn = {1558-3783},
year = {2017},
date = {2017-10-23},
journal = {IEEE Transactions on Automation Science and Engineering},
volume = {15},
number = {4},
pages = {1609-1620},
publisher = {IEEE},
abstract = {In this paper, an automatic vision-guided micromanipulation approach to facilitate versatile deployment and portable setup is proposed. This paper is motivated by the importance of micromanipulation and the limitations in existing automation technology in micromanipulation. Despite significant advancements in micromanipulation techniques, there remain bottlenecks in integrating and adopting automation for this application. An underlying reason for the gaps is the difficulty in deploying and setting up such systems. To address this, we identified two important design requirements, namely, portability and versatility of the micromanipulation platform. A self-contained vision-guided approach requiring no complicated preparation or setup is proposed. This is achieved through an uncalibrated self-initializing workflow algorithm also capable of assisted targeting. The feasibility of the solution is demonstrated on a low-cost portable microscope camera and compact actuated microstages. Results suggest subpixel accuracy in localizing the tool tip during initialization steps. The self-focus mechanism could recover intentional blurring of the tip by autonomously manipulating it 95.3% closer to the focal plane. The average error in visual servo is less than a pixel with our depth compensation mechanism showing better maintaining of similarity score in tracking. Cell detection rate in a 1637-frame video stream is 97.7% with subpixels localization uncertainty. Our work addresses the gaps in existing automation technology in the application of robotic vision-guided micromanipulation and potentially contributes to the way cell manipulation is performed.},
keywords = {Control Theory, Mechatronic Design, Physical System Modeling, Robot operated modular fixtures, Robotics & Automation},
pubstate = {published},
tppubtype = {article}
}
2016
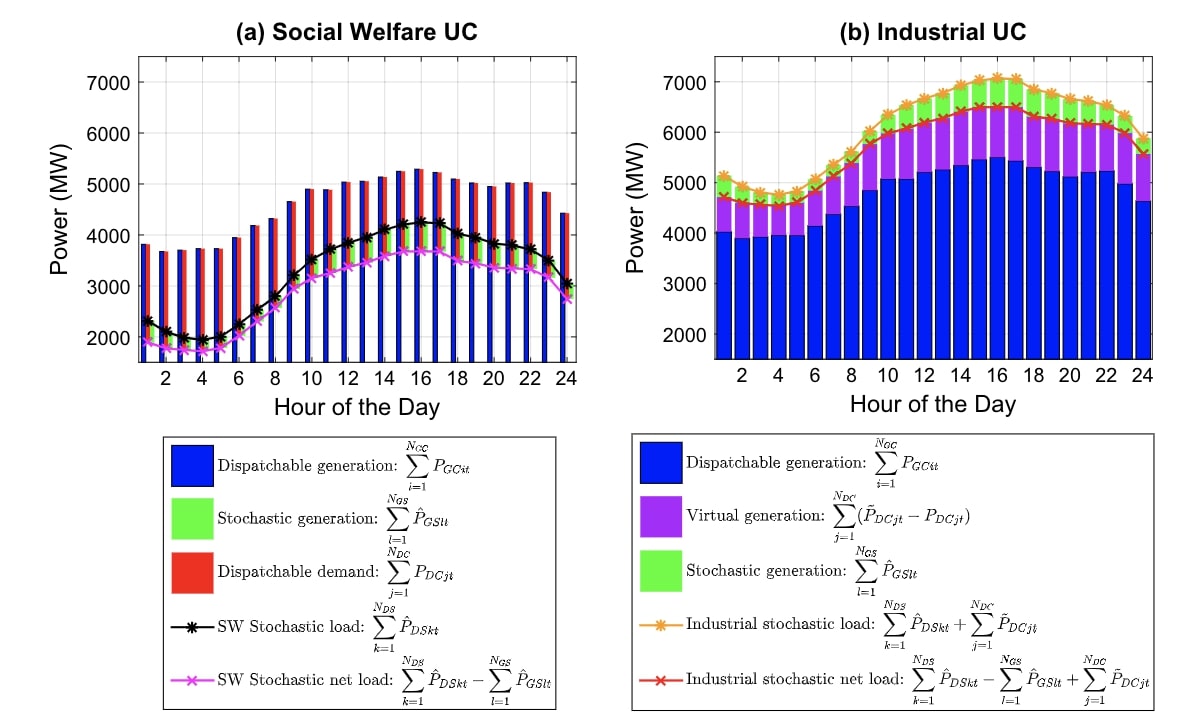
Bo Jiang; Aramazd Muzhikyan; Amro M Farid; Kamal Youcef-Toumi
Demand side management in power grid enterprise control: A comparison of industrial & social welfare approaches Journal Article
In: Applied Energy, vol. 187, pp. 833-846, 2016, ISSN: 0306-2619.
Abstract | Links | BibTeX | Tags: Algorithms, Control Theory, Experimentation, Robot operated modular fixtures, Robotics & Automation, Simulation
@article{MRL_AFM_Comparison_Industrial_Social_Welfare,
title = {Demand side management in power grid enterprise control: A comparison of industrial & social welfare approaches},
author = {Bo Jiang and Aramazd Muzhikyan and Amro M Farid and Kamal Youcef-Toumi},
url = {https://www.sciencedirect.com/science/article/pii/S0306261916315410},
doi = {https://doi.org/10.1016/j.apenergy.2016.10.096},
issn = {0306-2619},
year = {2016},
date = {2016-10-25},
journal = {Applied Energy},
volume = {187},
pages = {833-846},
publisher = {ScienceDirect},
abstract = {Despite the recognized importance of demand side management (DSM) for mitigating the impact of variable energy resources and reducing the system costs, the academic and industrial literature have taken divergent approaches to DSM implementation. The prequel to this paper has demonstrated that the netload baseline inflation – a feature particular to the industrial DSM unit commitment formulation – leads to higher and costlier day-ahead scheduling compared to the academic social welfare method. This paper now expands this analysis from a single optimization problem to the full power grid enterprise control with its multiple control layers at their associated time scales. These include unit commitment, economic dispatch and regulation services. It compares the two DSM formulations and quantifies the technical and economic impacts of industrial baseline errors in the day-ahead and real-time markets. The paper concludes that the presence of baseline errors – present only in the industrial model – leads to a cascade of additional system imbalances and costs as compared to the social welfare model. A baseline error introduced in the unit commitment problem will increase costs not just in the day-ahead market, but will also introduce a greater netload error residual in the real-time market causing additional cost and imbalances. These imbalances if left unmitigated degrade system reliability or otherwise require costly regulating reserves to achieve the same performance. An additional baseline error introduced in the economic dispatch further compounds this cascading effect with additional costs in the real-time market, amplified downstream imbalances, and further regulation capacity for its mitigation.},
keywords = {Algorithms, Control Theory, Experimentation, Robot operated modular fixtures, Robotics & Automation, Simulation},
pubstate = {published},
tppubtype = {article}
}
2011
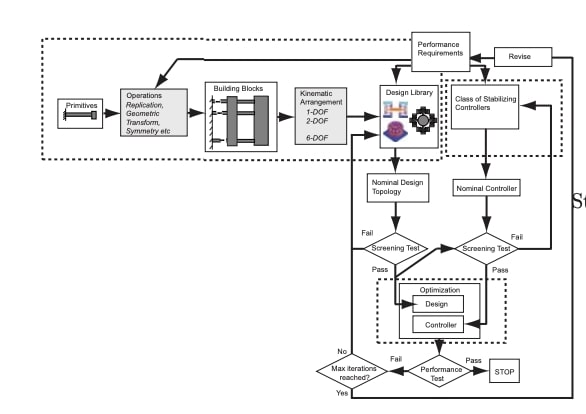
Vijay Shilpiekandula; Kamal Youcef-Toumi
Integrated Design and Control of Flexure-Based Nanopositioning Systems — Part I: Methodology Proceedings Article
In: pp. 9406-9412, IFAC, 2011, ISSN: 1474-6670, (18th IFAC World Congress).
Abstract | Links | BibTeX | Tags: Control Theory, Mechatronic Design, Nanotechnology, Physical System Modeling, Robot operated modular fixtures, Simulation
@inproceedings{MRL_AFM_Flexure_Nanopositioning_Methodology,
title = {Integrated Design and Control of Flexure-Based Nanopositioning Systems — Part I: Methodology},
author = {Vijay Shilpiekandula and Kamal Youcef-Toumi},
url = {https://www.sciencedirect.com/science/article/pii/S1474667016451232},
doi = {https://doi.org/10.3182/20110828-6-IT-1002.03796},
issn = {1474-6670},
year = {2011},
date = {2011-09-01},
journal = {IFAC Proceedings Volumes},
volume = {44},
number = {1},
pages = {9406-9412},
publisher = {IFAC},
abstract = {Abstract
Flexure-based mechanisms, also referred to as flexures, are widely being used as motion-guidance, or bearing, elements in applications requiring multi-degree-of-freedom positioning and alignment. Unlike friction-bearings (such as sliding or rolling contact bearings), flexures can be designed to offer, to a large extent, reliable linear elastic motion with a high resolution (on the order of nanometers) over small ranges of motion (on order of micrometers). Example applications include positioning a probe or sample in atomic force microscopy, alignment of tool and sample in stamping processes, and fine-positioning of wafers and masks in semiconductor manufacturing. These applications are often required satisfy critical functional requirements, such as load-capacity, bandwidth, resolution, and range. A systematic approach is needed to simultaneously address the design and control challenges involved, starting from the initial design concept generation stage to the final control implementation and testing. In this paper, we present an integrated design and control method for implementing flexure-based nanopositioning systems. We discuss the need for varying design topology and order of a controller in design and control optimization. An automation engine generates a set of flexure-based design topologies and also controllers of varying order in the optimization. A simple 1-DOF example is worked out to illustrate the steps involved in using this methodology. The outcome of the exercise is a novel design topology, with it shape and size optimized, and a controller synthesized such that a desired control bandwidth and design requirements of strength and modal separation are met.},
note = {18th IFAC World Congress},
keywords = {Control Theory, Mechatronic Design, Nanotechnology, Physical System Modeling, Robot operated modular fixtures, Simulation},
pubstate = {published},
tppubtype = {inproceedings}
}
Flexure-based mechanisms, also referred to as flexures, are widely being used as motion-guidance, or bearing, elements in applications requiring multi-degree-of-freedom positioning and alignment. Unlike friction-bearings (such as sliding or rolling contact bearings), flexures can be designed to offer, to a large extent, reliable linear elastic motion with a high resolution (on the order of nanometers) over small ranges of motion (on order of micrometers). Example applications include positioning a probe or sample in atomic force microscopy, alignment of tool and sample in stamping processes, and fine-positioning of wafers and masks in semiconductor manufacturing. These applications are often required satisfy critical functional requirements, such as load-capacity, bandwidth, resolution, and range. A systematic approach is needed to simultaneously address the design and control challenges involved, starting from the initial design concept generation stage to the final control implementation and testing. In this paper, we present an integrated design and control method for implementing flexure-based nanopositioning systems. We discuss the need for varying design topology and order of a controller in design and control optimization. An automation engine generates a set of flexure-based design topologies and also controllers of varying order in the optimization. A simple 1-DOF example is worked out to illustrate the steps involved in using this methodology. The outcome of the exercise is a novel design topology, with it shape and size optimized, and a controller synthesized such that a desired control bandwidth and design requirements of strength and modal separation are met.
0000
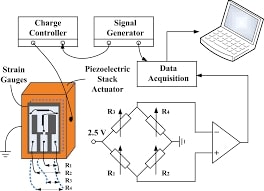
C Yang; C Li; F Xia; Y Zhu; J Zhao; K Youcef-Toumi
Charge Controller With Decoupled and Self-Compensating Configurations for Linear Operation of Piezoelectric Actuators in a Wide Bandwidth Journal Article
In: IEEE Transactions on Industrial Electronics, vol. 66, no. 7, pp. 5392-5402, 0000, ISSN: 1557-9948.
Abstract | Links | BibTeX | Tags: Control Theory, Instrumentation, Nanotechnology, Physical System Modeling, Robot operated modular fixtures, Visualization
@article{MRL_AFM_Charge_Controller_Compensating_Configs,
title = {Charge Controller With Decoupled and Self-Compensating Configurations for Linear Operation of Piezoelectric Actuators in a Wide Bandwidth},
author = {C Yang and C Li and F Xia and Y Zhu and J Zhao and K Youcef-Toumi},
url = {https://ieeexplore.ieee.org/document/8466119},
doi = {10.1109/TIE.2018.2868321},
issn = {1557-9948},
journal = {IEEE Transactions on Industrial Electronics},
volume = {66},
number = {7},
pages = {5392-5402},
abstract = {Charge control is a well-known sensorless approach to operate piezoelectric actuators, which has been proposed for more than 30 years. However, it is rarely used in industry because the implemented controllers suffer from the issues of limited low-frequency performance, long settling time, floating-load, and loss of stroke, etc. In this paper, a novel controller circuit dedicated to overcome these issues is presented. In the proposed scheme, a grounded-load charge controller with decoupled configuration is developed, which separates high-frequency and low-frequency paths, thus achieving arbitrarily low transition frequency without increasing the settling time. Based on this, a self-compensating configuration is further proposed and integrated into the controller circuit, which makes full use of controller output to improve its own control performance at low frequencies. Experimental results show that the presented charge controller can effectively reduce more than 88% of the hysteretic nonlinearity even when operating close to the transition frequency. To demonstrate its practical value, we then integrate it into a custom-designed high-speed atomic force microscope system. By comparing images obtained from using voltage drive and charge controller, it is clear that the piezoelectric hysteresis has been significantly reduced in a wide bandwidth.},
keywords = {Control Theory, Instrumentation, Nanotechnology, Physical System Modeling, Robot operated modular fixtures, Visualization},
pubstate = {published},
tppubtype = {article}
}