Mechatronics Research Lab Publications
List still being populated due to webpage maintenance
2019
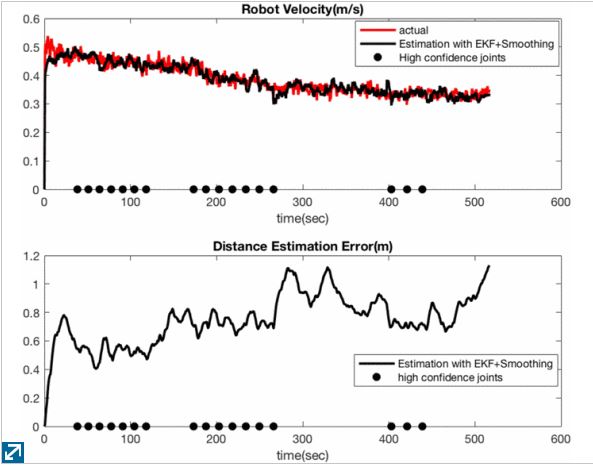
You Wu; Elizabeth Mittmann; Crystal Winston; Kamal Youcef-Toumi
A Practical Minimalism Approach to In-pipe Robot Localization Proceedings Article
In: 2019 American Control Conference (ACC), pp. 3180-3187, IEEE IEEE, 2019, ISBN: 978-1-5386-7926-5.
Abstract | Links | BibTeX | Tags: Algorithms, Computational Intelligence, Inspection; repair and intelligence for water distribution pipes, Physical System Modeling, Robotics & Automation, Simulation, Visualization
@inproceedings{MRL_WDP_Pipe_Robot_Localization,
title = {A Practical Minimalism Approach to In-pipe Robot Localization},
author = {You Wu and Elizabeth Mittmann and Crystal Winston and Kamal Youcef-Toumi},
url = {https://ieeexplore.ieee.org/document/8814648},
doi = {10.23919/ACC.2019.8814648},
isbn = {978-1-5386-7926-5},
year = {2019},
date = {2019-08-19},
booktitle = {2019 American Control Conference (ACC)},
pages = {3180-3187},
publisher = {IEEE},
organization = {IEEE},
abstract = {Water pipe leakage is a common and significant problem around the world. In recent years, an increasing amount of effort has been put into developing effective leak detection solutions for water pipes. Among them, the pressure gradient based method developed at the Massachusetts Institute of Technology excels for its sensitivity in low pressure, small diameter pipes. It can also work in both plastic and metallic pipes. However, in order for leaks detected to be fixed, one must also know the locations of the leaks. In addition, sensing the robot's location via GPS or remote sensors requires greater power and relies on certain ground properties. Thus this paper sets out to localize the robot using only the on board sensors which are an IMU, gyro, and the leak sensors. Through pipe joint measurement and the extended Kalman filter simulations show the tracking error is about 0.5% of the total distance of the robotic inspection. With a minimal number of additional leak sensors added, a complementary method was developed to function in more heavily tuberculated pipes.},
keywords = {Algorithms, Computational Intelligence, Inspection; repair and intelligence for water distribution pipes, Physical System Modeling, Robotics & Automation, Simulation, Visualization},
pubstate = {published},
tppubtype = {inproceedings}
}
2017
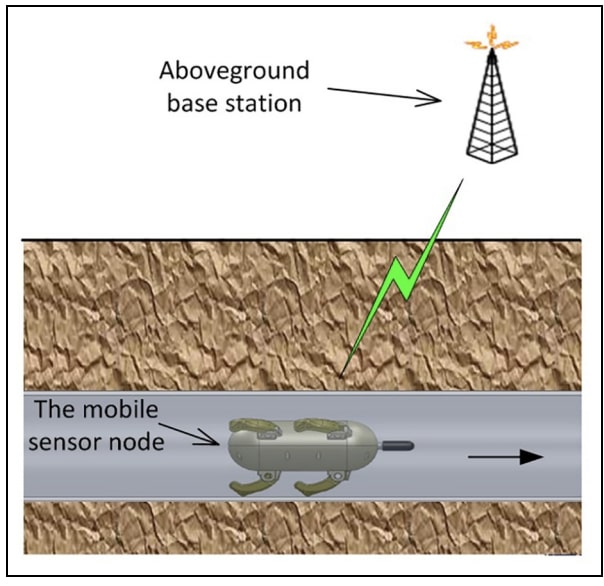
S Mekid; D Wu; R Hussain; K Youcef-Toumi
Channel modeling and testing of wireless transmission for underground in-pipe leak and material loss detection Journal Article
In: International Journal of Distributed Sensor Networks, vol. 13, no. 11, pp. 1550147717744715, 2017, ISSN: 1550147717744715.
Abstract | Links | BibTeX | Tags: Fabrication, Inspection, Inspection; repair and intelligence for water distribution pipes, Instrumentation, Mechatronic Design, Nanotechnology, Physical System Modeling
@article{MRL_AFM_Channel_Modeling,
title = {Channel modeling and testing of wireless transmission for underground in-pipe leak and material loss detection},
author = {S Mekid and D Wu and R Hussain and K Youcef-Toumi},
url = {https://doi.org/10.1177/1550147717744715},
doi = {10.1177/1550147717744715},
issn = {1550147717744715},
year = {2017},
date = {2017-01-01},
journal = {International Journal of Distributed Sensor Networks},
volume = {13},
number = {11},
pages = {1550147717744715},
publisher = {Sage},
abstract = {A systematic real-time methodology is adopted for leak detection in underground buried pipes. The wireless communication system is used to analyze the system performance based on the received power by monopole antenna deployed at the receiving side. Instrumentation designed for underground measurement and control such as leak and materials loss detection needs wireless communications to aboveground in both ways and in real-time mode. This constitutes one of the timely and challenging issues of battery-operated systems. The purpose of this work is to characterize the radio transmission between underground buried pipes and base station using multi-layer media including both theoretical and experimental approaches by utilizing various modulation schemes. The objective is to identify the range of operating communication frequencies having lower energy loss, lower resulting bit error rate, and the power needed to transfer packets designed to carry data through the media. This will support the on-device power management to secure large autonomy operations. Experimental tests have shown that the overall received energy was mixed with ambient energy if the latter is sent at the same frequency and that the optimum frequency range used to transmit energy was rather at low frequency range of 100–200 MHz.},
keywords = {Fabrication, Inspection, Inspection; repair and intelligence for water distribution pipes, Instrumentation, Mechatronic Design, Nanotechnology, Physical System Modeling},
pubstate = {published},
tppubtype = {article}
}
2015
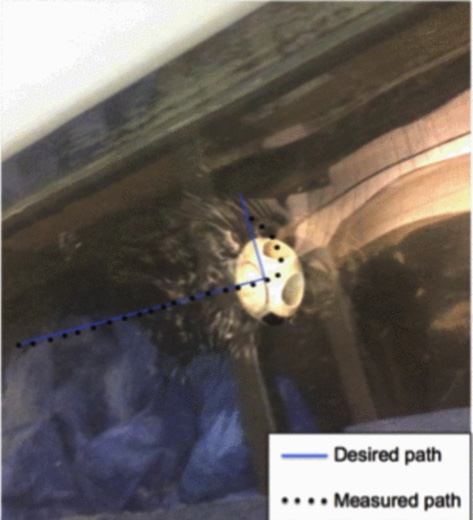
You Wu; Antoine Noel; David Donghyun Kim; Kamal Youcef-Toumi; Rached Ben-Mansour
Design of a maneuverable swimming robot for in-pipe missions Proceedings Article
In: 2015 IEEE/RSJ International Conference on Intelligent Robots and Systems (IROS), pp. 4864-4871, IEEE IEEE, 2015, ISBN: 978-1-4799-9994-1.
Abstract | Links | BibTeX | Tags: Experimentation, Inspection; repair and intelligence for water distribution pipes, intelligent systems, Physical System Modeling, Simulation, Visualization
@inproceedings{MRL_WDP_In_Pipe_Missions,
title = {Design of a maneuverable swimming robot for in-pipe missions},
author = {You Wu and Antoine Noel and David Donghyun Kim and Kamal Youcef-Toumi and Rached Ben-Mansour},
url = {https://ieeexplore.ieee.org/document/7354061},
doi = {10.1109/IROS.2015.7354061},
isbn = {978-1-4799-9994-1},
year = {2015},
date = {2015-12-17},
booktitle = {2015 IEEE/RSJ International Conference on Intelligent Robots and Systems (IROS)},
pages = {4864-4871},
publisher = {IEEE},
organization = {IEEE},
abstract = {Autonomous underwater robots provide opportunities to perform missions in confined environments such as water pipe networks. They can carry sensors in these pipes and perform tasks such as mapping and inspection. Those robots must have a high level of maneuverability in order to navigate through complex networks of pipes with irregularities due to rust and calcite deposition. We propose a fully integrated, untethered robot capable of carrying sensors and maneuver into water pipe networks. The objective of this paper is to present (i) the optimal shape design and (ii) a propulsion system selection and sizing procedure for such robots. A prototype is built to demonstrate the basic elements of maneuverability, including following straight lines and making sharp turns.},
keywords = {Experimentation, Inspection; repair and intelligence for water distribution pipes, intelligent systems, Physical System Modeling, Simulation, Visualization},
pubstate = {published},
tppubtype = {inproceedings}
}
2014
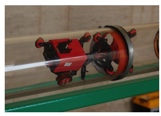
Dimitris Chatzigeorgiou; You Wu; Kamal Youcef-Toumi; Rached Ben-Mansour
MIT Leak Detector: An in-pipe leak detection robot Proceedings Article
In: 2014 IEEE International Conference on Robotics and Automation (ICRA), pp. 2091-2091, IEEE IEEE, 2014, ISBN: 978-1-4799-3685-4.
Abstract | Links | BibTeX | Tags: Inspection; repair and intelligence for water distribution pipes, Physical Systems Modeling, Robotics & Automation, Simulation, Visualization
@inproceedings{MRL_WDP_Leak_Detecting_Robot,
title = {MIT Leak Detector: An in-pipe leak detection robot},
author = {Dimitris Chatzigeorgiou and You Wu and Kamal Youcef-Toumi and Rached Ben-Mansour},
url = {https://ieeexplore.ieee.org/document/6907144},
doi = {10.1109/ICRA.2014.6907144},
isbn = {978-1-4799-3685-4},
year = {2014},
date = {2014-09-24},
booktitle = {2014 IEEE International Conference on Robotics and Automation (ICRA)},
pages = {2091-2091},
publisher = {IEEE},
organization = {IEEE},
abstract = {In this work we present a new in-pipe leak detection robot, the MIT Leak Detector. The system performs autonomous leak detection in gas pipes in a reliable and robust fashion. Detection in based on the presence of a pressure gradient in the neighborhood of the leak. As the MIT Leak Detector travels through pipes, it picks up the pressure gradient in case of leaks via a carefully designed detector. In this work we demonstrate the performance of the system in a lab setup, which consists of 100mm ID pipes containing pressurized air.},
keywords = {Inspection; repair and intelligence for water distribution pipes, Physical Systems Modeling, Robotics & Automation, Simulation, Visualization},
pubstate = {published},
tppubtype = {inproceedings}
}
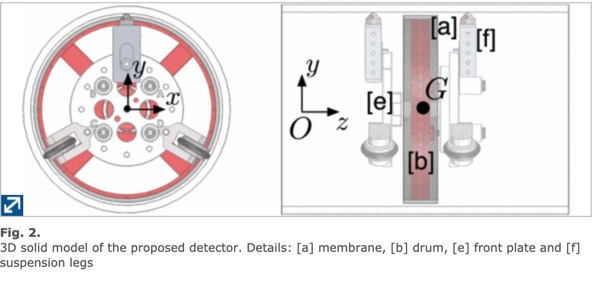
Dimitris Chatzigeorgiou; Kamal Youcef-Toumi; Rached Ben-Mansour
Modeling and analysis of an in-pipe robotic leak detector Proceedings Article
In: 2014 IEEE International Conference on Robotics and Automation (ICRA), pp. 3351-3357, IEEE, 2014, ISBN: 978-1-4799-3685-4.
Abstract | Links | BibTeX | Tags: Inspection; repair and intelligence for water distribution pipes, Physical Systems Modeling, Robotics & Automation, Simulation, Visualization
@inproceedings{MRL_WDP_Analysis_Leak_Detection,
title = {Modeling and analysis of an in-pipe robotic leak detector},
author = {Dimitris Chatzigeorgiou and Kamal Youcef-Toumi and Rached Ben-Mansour},
url = {https://ieeexplore.ieee.org/abstract/document/6907341},
doi = {10.1109/ICRA.2014.6907341},
isbn = {978-1-4799-3685-4},
year = {2014},
date = {2014-09-24},
booktitle = {2014 IEEE International Conference on Robotics and Automation (ICRA)},
pages = {3351-3357},
publisher = {IEEE},
abstract = {Leakage is the most important factor for unaccounted losses in any pipe network around the world. Most state of the art leak detection systems have limited applicability, lack in reliability and depend on user experience for data extraction. This paper is about a novel system for robotic pipe integrity inspection. Unlike existing systems, detection in based on the presence of a pressure gradient in the neighborhood of a leak. This phenomenon is translated into force measurements via a specially designed and instrumented mechanical embodiment (detector). In this paper an analytic dynamic model of the robotic detector is derived and studied. A prototype is built and the main concepts are validated via experiments.},
keywords = {Inspection; repair and intelligence for water distribution pipes, Physical Systems Modeling, Robotics & Automation, Simulation, Visualization},
pubstate = {published},
tppubtype = {inproceedings}
}
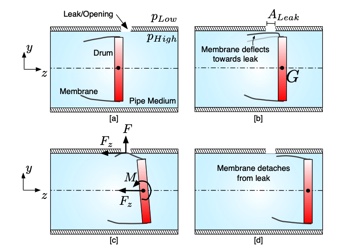
Dimitris Chatzigeorgiou; Kamal Youcef-Toumi; Rached Ben-Mansour
Detection estimation algorithms for in-pipe leak detection Proceedings Article
In: 2014 American Control Conference, pp. 5508-5514, 2014, ISBN: 978-1-4799-3274-0.
Abstract | Links | BibTeX | Tags: Algorithms, Control Theory, Experimentation, Inspection; repair and intelligence for water distribution pipes, Physical System Modeling, Robotics and Automation, Simulation
@inproceedings{MRL_WDP_Estimation_Algorithms,
title = {Detection estimation algorithms for in-pipe leak detection},
author = {Dimitris Chatzigeorgiou and Kamal Youcef-Toumi and Rached Ben-Mansour},
url = {https://ieeexplore.ieee.org/document/6859203},
doi = {10.1109/ACC.2014.6859203},
isbn = {978-1-4799-3274-0},
year = {2014},
date = {2014-07-21},
booktitle = {2014 American Control Conference},
pages = {5508-5514},
abstract = {Leakage is the most important factor for unaccounted losses in any pipe network around the world. However, most state of the art leak detection systems have limited applicability, lack in reliability and/or depend on user experience for data interpretation. In this paper we present a new, autonomous, in-pipe, leak detection system. The detection principle is based on the presence of a pressure gradient in the neighborhood of a leak in a pressurized pipe. This phenomenon is translated into force measurements via a carefully designed and instrumented mechanical embodiment (MIT Leak Detector). We then introduce a detection and estimation scheme. The latter one allows not only for the reliable detection, but also for the estimation of the incidence angle and the magnitude of the forces that are associated with the leak. Finally, a prototype is built and experiments in pipes are conducted to demonstrate the efficacy of the proposed methodology.},
keywords = {Algorithms, Control Theory, Experimentation, Inspection; repair and intelligence for water distribution pipes, Physical System Modeling, Robotics and Automation, Simulation},
pubstate = {published},
tppubtype = {inproceedings}
}
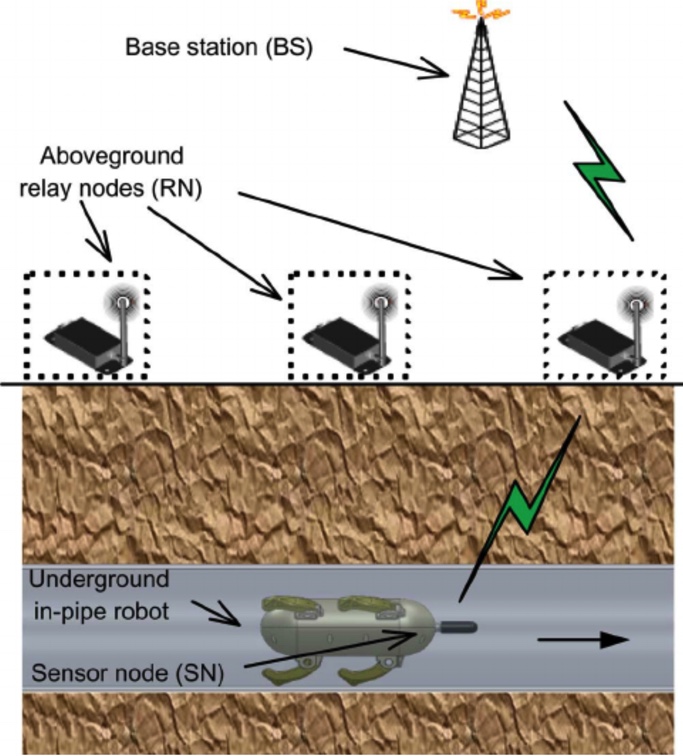
Dalei Wu; Dimitris Chatzigeorgiou; Kamal Youcef-Toumi; Samir Mekid; Rached Ben-Mansour
Channel-Aware Relay Node Placement in Wireless Sensor Networks for Pipeline Inspection Proceedings Article
In: Proceedings of the American Control Conference (2013), ACC ACC, 2014, ISSN: 1536-1276.
Abstract | Links | BibTeX | Tags: Inspection; repair and intelligence for water distribution pipes, Physical System Modeling, Robotics & Automation, Simulation, Visualization
@inproceedings{MRL_WDP_Node_Pipeline_Inspection,
title = {Channel-Aware Relay Node Placement in Wireless Sensor Networks for Pipeline Inspection},
author = {Dalei Wu and Dimitris Chatzigeorgiou and Kamal Youcef-Toumi and Samir Mekid and Rached Ben-Mansour},
url = {https://www.researchgate.net/publication/261282962_Channel-Aware_Relay_Node_Placement_in_Wireless_Sensor_Networks_for_Pipeline_Inspection},
doi = {10.1109/TWC.2014.2314120},
issn = {1536-1276},
year = {2014},
date = {2014-03-24},
booktitle = {Proceedings of the American Control Conference (2013)},
publisher = {ACC},
organization = {ACC},
abstract = {Wireless sensor networks (WSNs) provide an effective approach for underground pipeline inspection. Such WSNs comprise of sensor nodes (SNs) and relay nodes (RNs) for information sensing and communication. WSNs can perform accurate and realtime inspection, especially in adverse environments. However, transmitting information between underground and aboveground nodes is very challenging due to the mobility and limited energy supply of the SNs as well as complex radio propagation environment. Therefore, proper deployment of a WSN is critical to provide reliable communications and efficient inspection. This paper presents a methodology for deploying aboveground RNs in WSNs. Specifically, it provides an optimum placement of RNs along with energy use so as to allow reliable communications. This method takes into account characteristics of the wireless channels, energy consumption, pipeline coverage requirements, and SN's transmission power levels. The paper provides a path loss model for radio propagation over multiple transmission media and an algorithm for optimization of RN placement and SN's transmission power. Simulation results show the efficacy of the proposed framework.},
keywords = {Inspection; repair and intelligence for water distribution pipes, Physical System Modeling, Robotics & Automation, Simulation, Visualization},
pubstate = {published},
tppubtype = {inproceedings}
}
2013
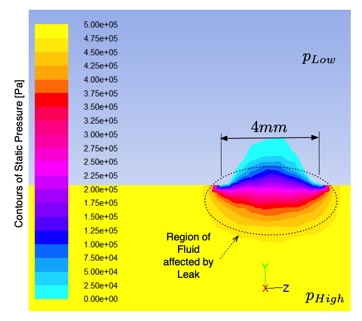
Apoorva Santhosh; Amro M Farid; Kamal Youcef-Toumi
Design and Evaluation of an In-Pipe Leak Detection Sensing Technique Based on Force Transduction Proceedings Article
In: ASME 2012 International Mechanical Engineering Congress and Exposition, IEEE IEEE, 2013, ISBN: 978-0-7918-4520-2.
Abstract | Links | BibTeX | Tags: Algorithms, Computational Intelligence, Inspection; repair and intelligence for water distribution pipes, Physical System Modeling, Robotics & Automation, Simulation, Visualization
@inproceedings{MRL_WDP_Force_Transduction_Leaking,
title = {Design and Evaluation of an In-Pipe Leak Detection Sensing Technique Based on Force Transduction},
author = {Apoorva Santhosh and Amro M Farid and Kamal Youcef-Toumi},
url = {https://asmedigitalcollection.asme.org/IMECE/proceedings/IMECE2012/45202/489/254570},
doi = {10.1115/IMECE2012-87493},
isbn = {978-0-7918-4520-2},
year = {2013},
date = {2013-10-08},
booktitle = {ASME 2012 International Mechanical Engineering Congress and Exposition},
publisher = {IEEE},
organization = {IEEE},
abstract = {Leakage is the major factor for unaccounted fluid losses in almost every pipe network. In most cases the deleterious effects associated with the occurrence of leaks may present serious economical and health problems and therefore, leaks must be quickly detected, located and repaired. The problem of leakage becomes even more serious when it is concerned with the vital supply of fresh water to the community. Leaking water pipelines can develop large health threats to people mostly because of the infiltration of contaminants into the water network. Such possibilities of environmental health disasters have spurred research into the development of methods for pipeline leakage detection. Most state of the art leak detection techniques have limited applicability, while some of them are not reliable enough and sometimes depend on user experience. Our goal in this work is to design and develop a reliable leak detection sensing system. The proposed technology utilizes the highly localized pressure gradient in the vicinity of a small opening due to leakage in a pressurized pipeline. In this paper we study this local phenomenon in detail and try to understand it with the help of numerical simulations in leaking pipelines (CFD studies). Finally a new system for leak detection is presented. The proposed system is designed in order to reduce the number of sensing elements required for detection. The main concept and detailed design are laid out. A prototype is fabricated and presented as a proof of concept. The prototype is tested in a simple experimental setup with artificial leakages for experimental evaluation. The sensing technique discussed in this work can be deployed in water, oil and gas pipelines without significant changes in the design, since the concepts remain the same in all cases.},
keywords = {Algorithms, Computational Intelligence, Inspection; repair and intelligence for water distribution pipes, Physical System Modeling, Robotics & Automation, Simulation, Visualization},
pubstate = {published},
tppubtype = {inproceedings}
}
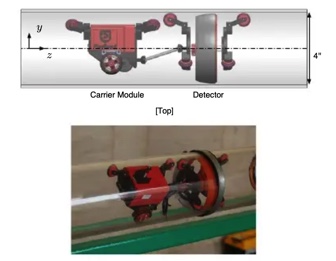
Dimitris Chatzigeorgiou; You Wu; Kamal Youcef-Toumi; Rached Ben-Mansour
Reliable Sensing of Leaks in Pipelines Proceedings Article
In: AWWA Annual Conference and Exposition, 2014, ASME ASME, 2013, ISBN: 978-0-7918-5613-0.
Abstract | Links | BibTeX | Tags: Inspection; repair and intelligence for water distribution pipes, Physical Systems Modeling, Robotics & Automation, Simulation, Visualization
@inproceedings{MRL_WDP_Reliable_Leak_Sensing,
title = {Reliable Sensing of Leaks in Pipelines},
author = {Dimitris Chatzigeorgiou and You Wu and Kamal Youcef-Toumi and Rached Ben-Mansour},
url = {https://www.academia.edu/8791279/Chatzigeorgiou_D._Wu_Y._Youcef-Toumi_K._and_Ben-Mansour_R._Reliable_Sensing_of_Leaks_in_Pipelines_ASME_Dynamic_Systems_and_Control_Conference_2013},
isbn = {978-0-7918-5613-0},
year = {2013},
date = {2013-01-01},
booktitle = {AWWA Annual Conference and Exposition, 2014},
publisher = {ASME},
organization = {ASME},
abstract = {Leakage is the major factor for unaccounted losses in every pipe network around the world (oil, gas or water). In most cases the deleterious effects associated with the occurrence of leaks may present serious economical and health problems. Therefore, leaks must be quickly detected, located and repaired. Unfortunately, most state of the art leak detection systems have limited applicability, are neither reliable nor robust, while others depend on user experience. In this work we present a new in-pipe leak detection system, PipeGuard. PipeGuard performs autonomous leak detection in pipes and, thus, eliminates the need for user experience. This paper focuses on the detection module and its main characteristics. Detection in based on the presence of a pressure gradient in the neighborhood of the leak. Moreover, the proposed detector can sense leaks at any angle around the circumference of the pipe with only two sensors. We have validated the concepts by building a prototype and evaluated its performance under real conditions in an experimental laboratory setup.},
keywords = {Inspection; repair and intelligence for water distribution pipes, Physical Systems Modeling, Robotics & Automation, Simulation, Visualization},
pubstate = {published},
tppubtype = {inproceedings}
}
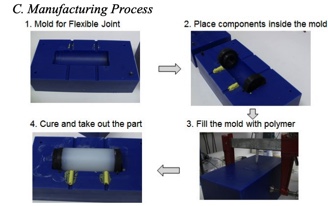
Changrak Choi; Kamal Youcef-Toumi
Robot design for high flow liquid pipe networks Proceedings Article
In: 2013 IEEE/RSJ International Conference onIntelligent Robots and Systems (IROS), pp. 246-251, IEEE IEEE, 2013.
Abstract | Links | BibTeX | Tags: Experimentation, Fabrication, Inspection; repair and intelligence for water distribution pipes, Physical System Modeling, Robotics & Automation, Simulation
@inproceedings{MRL_WDP_High_Flow_Pipe_Robot,
title = {Robot design for high flow liquid pipe networks},
author = {Changrak Choi and Kamal Youcef-Toumi},
url = {https://ieeexplore.ieee.org/stamp/stamp.jsp?tp=&arnumber=6696360&isnumber=6696319},
doi = {10.1109/IROS.2013.6696360},
year = {2013},
date = {2013-01-01},
booktitle = {2013 IEEE/RSJ International Conference onIntelligent Robots and Systems (IROS)},
pages = {246-251},
publisher = {IEEE},
organization = {IEEE},
abstract = {In-pipe robots are important for inspection of pipe network that form vital infrastructure of modern society. Nevertheless, most in-pipe robots developed so far are targeted at working inside gas pipes and not suitable for liquid pipes. This paper presents a new approach for designing in-pipe robot to work inside a liquid environment in the presence of high drag forces. Three major subsystems - propulsion, braking, and turning - are described in detail with new concepts and mechanisms that differ from conventional in-pipe robots. Prototypes of each subsystem are designed, built and tested for validation. Resulting is a robot design that navigates efficiently inside liquid pipe network and can be used for practical inspection purposes.},
keywords = {Experimentation, Fabrication, Inspection; repair and intelligence for water distribution pipes, Physical System Modeling, Robotics & Automation, Simulation},
pubstate = {published},
tppubtype = {inproceedings}
}
2012
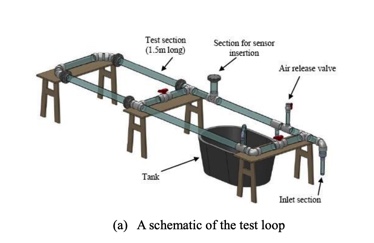
Atia E Khalifa; Rached Ben-Mansour; Kamal Youcef-Toumi; Changrak Choi
Characterization of In-Pipe Acoustic Wave for Water Leak Detection Proceedings Article
In: ASME 2011 International Mechanical Engineering Congress and Exposition, pp. 995-1000, ACC ACC, 2012, ISBN: 978-0-7918-5494-5.
Abstract | Links | BibTeX | Tags: Algorithms, Computational Intelligence, Inspection; repair and intelligence for water distribution pipes, Physical System Modeling, Robotics & Automation, Simulation, Visualization
@inproceedings{MRL_WDP_Acoustic_Wave_Pipe_Leakage,
title = {Characterization of In-Pipe Acoustic Wave for Water Leak Detection},
author = {Atia E Khalifa and Rached Ben-Mansour and Kamal Youcef-Toumi and Changrak Choi},
url = {https://asmedigitalcollection.asme.org/IMECE/proceedings/IMECE2011/54945/995/355499},
doi = {10.1115/IMECE2011-62333},
isbn = {978-0-7918-5494-5},
year = {2012},
date = {2012-08-01},
booktitle = {ASME 2011 International Mechanical Engineering Congress and Exposition},
pages = {995-1000},
publisher = {ACC},
organization = {ACC},
abstract = {This paper presents experimental observations on the characteristics of the acoustic signal propagation and attenuation inside water-filled pipes. An acoustic source (exciter) is mounted on the internal pipe wall, at a fixed location, and produces a tonal sound to simulate a leak noise with controlled frequency and amplitude, under different flow conditions. A hydrophone is aligned with the pipe centerline and can be re-positioned to capture the acoustic signal at different locations. Results showed that the wave attenuation depends on the source frequency and the line pressure. High frequency signals get attenuated more with increasing distance from the source. The optimum location to place the hydrophone for capturing the acoustic signal is not at the vicinity of source location. The optimum location also depends on the frequency and line pressure. It was also observed that the attenuation of the acoustic waves is higher in more flexible pipes like PVC ones.},
keywords = {Algorithms, Computational Intelligence, Inspection; repair and intelligence for water distribution pipes, Physical System Modeling, Robotics & Automation, Simulation, Visualization},
pubstate = {published},
tppubtype = {inproceedings}
}
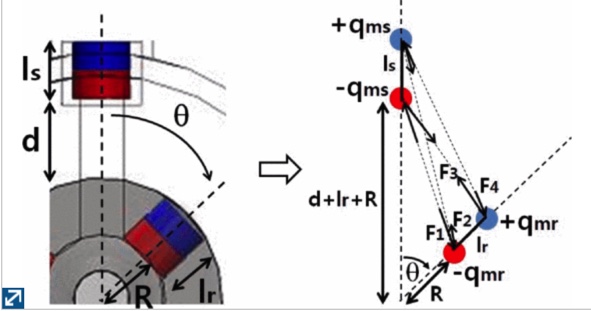
C Choi; D Chatzigeorgiou; R Ben-Mansour; K Youcef-Toumi
Design and analysis of novel friction controlling mechanism with minimal energy for in-pipe robot applications Proceedings Article
In: 2012 IEEE International Conference on Robotics and Automation, pp. 4118-4123, IEEE IEEE, 2012, ISBN: 978-1-4673-1405-3.
Abstract | Links | BibTeX | Tags: Experimentation, Fabrication, Inspection; repair and intelligence for water distribution pipes, Physical System Modeling, Robotics and Automation, Simulation, Visualization
@inproceedings{MRL_WDP_Friction_Minimization,
title = {Design and analysis of novel friction controlling mechanism with minimal energy for in-pipe robot applications},
author = {C Choi and D Chatzigeorgiou and R Ben-Mansour and K Youcef-Toumi},
url = {https://ieeexplore.ieee.org/document/6225380},
doi = {10.1109/ICRA.2012.6225380},
isbn = {978-1-4673-1405-3},
year = {2012},
date = {2012-06-28},
booktitle = {2012 IEEE International Conference on Robotics and Automation},
pages = {4118-4123},
publisher = {IEEE},
organization = {IEEE},
abstract = {In-pipe wheeled robots require friction on the wheels to maintain traction. Ability to vary this friction is highly desirable but conventionally used linkage mechanism is not suitable for it. This paper presents a novel mechanism generating adjustable friction with minimal energy consumption for in-pipe robots. The mechanism uses permanent magnets to achieve the objective. An appropriate model for the system is also presented and discussed. The paper identifies the important design parameters, and more importantly establishes the relation between the design parameters and the system's performance. In addition, a prototype of the mechanism was designed, fabricated and tested for validation.},
keywords = {Experimentation, Fabrication, Inspection; repair and intelligence for water distribution pipes, Physical System Modeling, Robotics and Automation, Simulation, Visualization},
pubstate = {published},
tppubtype = {inproceedings}
}
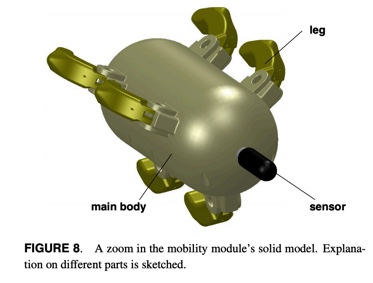
Dimitris M Chatzigeorgiou; Atia E Khalifa; Kamal Youcef-Toumi; Rached Ben-Mansour
An In-Pipe Leak Detection Sensor: Sensing Capabilities and Evaluation Proceedings Article
In: ASME 2011 International Design Engineering Technical Conferences and Computers and Information in Engineering Conference, pp. 481-489, ACC ACC, 2012, ISBN: 978-0-7918-5480-8.
Abstract | Links | BibTeX | Tags: Algorithms, Computational Intelligence, Inspection; repair and intelligence for water distribution pipes, Physical System Modeling, Robotics & Automation, Simulation, Visualization
@inproceedings{MRL_WDP_Leak_Capability_Sensor,
title = {An In-Pipe Leak Detection Sensor: Sensing Capabilities and Evaluation},
author = {Dimitris M Chatzigeorgiou and Atia E Khalifa and Kamal Youcef-Toumi and Rached Ben-Mansour},
url = {https://asmedigitalcollection.asme.org/IDETC-CIE/proceedings/IDETC-CIE2011/54808/481/351961},
doi = {10.1115/DETC2011-48411},
isbn = {978-0-7918-5480-8},
year = {2012},
date = {2012-06-12},
booktitle = {ASME 2011 International Design Engineering Technical Conferences and Computers and Information in Engineering Conference},
pages = {481-489},
publisher = {ACC},
organization = {ACC},
abstract = {In most cases the deleterious effects associated with the occurrence of leak may present serious problems and therefore leaks must be quickly detected, located and repaired. The problem of leakage becomes even more serious when it is concerned with the vital supply of fresh water to the community. In addition to waste of resources, contaminants may infiltrate into the water supply. The possibility of environmental health disasters due to delay in detection of water pipeline leaks has spurred research into the development of methods for pipeline leak and contamination detection. Leaks in water pipes create acoustic emissions, which can be sensed to identify and localize leaks. Leak noise correlators and listening devices have been reported in the literature as successful approaches to leak detection but they have practical limitations in terms of cost, sensitivity, reliability and scalability. To overcome those limitations the development of an in-pipe traveling leak detection system is proposed. The development of such a system requires a clear understanding of acoustic signals generated from leaks and the study of the variation of those signals with different pipe loading conditions, leak sizes and surrounding media. This paper discusses those signals and evaluates the merits of an in-pipe-floating sensor.},
keywords = {Algorithms, Computational Intelligence, Inspection; repair and intelligence for water distribution pipes, Physical System Modeling, Robotics & Automation, Simulation, Visualization},
pubstate = {published},
tppubtype = {inproceedings}
}
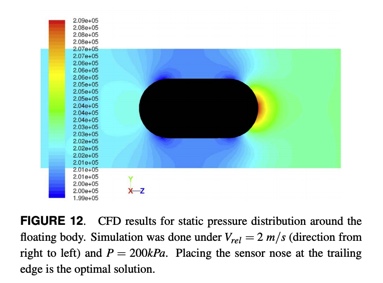
Dimitris M Chatzigeorgiou; Kamal Youcef-Toumi; Atia E Khalifa; Rached Ben-Mansour
Analysis and Design of an In-Pipe System for Water Leak Detection Proceedings Article
In: ASME 2011 International Design Engineering Technical Conferences and Computers and Information in Engineering Conference, pp. 1007-1016, ASME ASME, 2012, ISBN: 978-0-7918-5482-2.
Abstract | Links | BibTeX | Tags: Algorithms, Computational Intelligence, Inspection; repair and intelligence for water distribution pipes, Physical System Modeling, Robotics & Automation, Simulation, Visualization
@inproceedings{MRL_WDP_Design_Water_Leak_Detection,
title = {Analysis and Design of an In-Pipe System for Water Leak Detection},
author = {Dimitris M Chatzigeorgiou and Kamal Youcef-Toumi and Atia E Khalifa and Rached Ben-Mansour},
url = {https://asmedigitalcollection.asme.org/IDETC-CIE/proceedings/IDETC-CIE2011/54822/1007/353866},
doi = {10.1115/DETC2011-48395},
isbn = {978-0-7918-5482-2},
year = {2012},
date = {2012-06-12},
booktitle = {ASME 2011 International Design Engineering Technical Conferences and Computers and Information in Engineering Conference},
pages = {1007-1016},
publisher = {ASME},
organization = {ASME},
abstract = {In most cases the deleterious effects associated with the occurrence of leaks may present serious problems and therefore, leaks must be quickly detected, located and repaired. The problem of leakage becomes even more serious when it is concerned with the vital supply of fresh water to the community. In addition to waste of resources, contaminants may infiltrate into the water supply. The possibility of environmental health disasters due to delay in detection of water pipeline leaks has spurred research into the development of methods for pipeline leak and contamination detection. Leaking in water networks has been a very significant problem worldwide, especially in developing countries, where water is sparse. Many different techniques have been developed to detect leaks, either from the inside or from the outside of the pipe; each one of them with their advantages, complexities but also limitations. To overcome those limitations we focus our work on the development of an in-pipe-floating sensor. The present paper discusses the design considerations of a novel autonomous system for in-pipe water leak detection. The system is carefully designed to be minimally invasive to the flow within the pipe and thus not to affect the delicate leak signal. One of its characteristics is the controllable motion inside the pipe. The system is capable of pinpointing leaks in pipes while operating in real network conditions, i.e. pressurized pipes and high water flow rates, which are major challenges.},
keywords = {Algorithms, Computational Intelligence, Inspection; repair and intelligence for water distribution pipes, Physical System Modeling, Robotics & Automation, Simulation, Visualization},
pubstate = {published},
tppubtype = {inproceedings}
}
2010
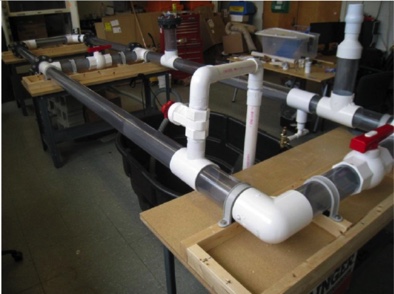
Dimitris M Chatzigeorgiou; Sumeet Kumar; Atia E Khalifa; Ajay Deshpande; Kamal Youcef-Toumi; Sanjay Sarma; Rached Ben-Mansour
In-pipe Acoustic Characterization of Leak Signals in Plastic Water-filled Pipes Proceedings Article
In: AWWA Annual Conference and Exposition (ACE) 2010, AWWA AWWA, 2010.
Abstract | Links | BibTeX | Tags: Algorithms, Computational Intelligence, Inspection; repair and intelligence for water distribution pipes, Physical System Modeling, Robotics & Automation, Simulation, Visualization
@inproceedings{MRL_WDP_Acoustic_Leak_Signals,
title = {In-pipe Acoustic Characterization of Leak Signals in Plastic Water-filled Pipes},
author = {Dimitris M Chatzigeorgiou and Sumeet Kumar and Atia E Khalifa and Ajay Deshpande and Kamal Youcef-Toumi and Sanjay Sarma and Rached Ben-Mansour},
url = {https://www.researchgate.net/publication/277303127_In-pipe_Acoustic_Characterization_of_Leak_Signals_in_Plastic_Water-filled_Pipes},
year = {2010},
date = {2010-01-01},
booktitle = {AWWA Annual Conference and Exposition (ACE) 2010},
publisher = {AWWA},
organization = {AWWA},
abstract = {Acoustic emissions can be sensed to identify and localize leaks in water pipes. Leak noise correlators and listening devices have been reported in literature as successful approaches to leak detection but they have practical limitations in terms of cost, sensitivity, reliability and scalability. A possible efficient solution is the development of an in-pipe traveling leak detection system. It has been reported that in-pipe sensing is more accurate and efficient since the sensing element can be very close to the sound source. Currently in-pipe approaches are limited to large leaks and larger diameter pipes. Development of such a system requires clear understanding of acoustic signals generated from leaks and their variation with different pipe loading conditions, leak sizes and surrounding media. This paper discusses the acoustic characterization of leak signals in controlled environments. A lab experimental setup was designed and built in which measurements were taken from inside 4 inch PVC water pipes using a hydrophone. Signals were collected for a wide range of conditions: different pressures and leak flow rates to better understand the leak signal signatures. Experiments were conducted with different pipe connecting elements like valves and junctions, and different external conditions such as pipes placed in water, air and soil. Signals were collected at various distances from the leak location (upstream and downstream) to understand the opportunities of spatial cross-correlation techniques in localizing leaks and the effect of sensor position on the signal. Characterizations of different datasets are presented in frequency domain. The implications of acoustic characterization on the design of algorithms for leak detection are discussed and a simple algorithm to decide whether or not a leak is present near the sensor location is proposed, based on signal power calculations. The characterization gives insights, which will pave ways for the development of smart, autonomous pipe-traversing systems capable of detecting and localizing leaks on a city level water distribution network.},
keywords = {Algorithms, Computational Intelligence, Inspection; repair and intelligence for water distribution pipes, Physical System Modeling, Robotics & Automation, Simulation, Visualization},
pubstate = {published},
tppubtype = {inproceedings}
}